By the end of this decade, most companies making consumer-facing goods will have a problem. To fulfill their promises to lower greenhouse gas emissions in their supply chains by 2030, they’ll be scrambling to find low-carbon goods and materials. But based on current production pipelines, the supply of green materials will fall far short of demand. We call this “sustainability scarcity.”
A technology revolution unfolding in the chemicals industry could be an important part of the solution. It involves making pretty much every chemical-based product we use today, from the fabrics we wear to our shampoo and plastic bottles, not from hydrocarbons extracted from the earth but from carbon dioxide removed from the atmosphere or recycled from industrial processes. This process, known as CO2 to X, or CO2 transformation, can not only help companies slash their greenhouse-gas footprints. It can also enable them to make products that are “carbon negative,” or “nature positive.”
Scientists and the petrochemicals industry have been working for decades to find ways to turn CO2 into something useful, rather than just storing it in holes in the ground. Now, certain CO2 to X products are becoming commercially viable, due to advances in materials science, process engineering, the wider availability of hydrogen and renewables, rising investment, and growing customer appetite.
Scientists and the petrochemicals industry have been working for decades to find ways to turn CO2 into something useful, rather than just storing it in holes in the ground. Now, certain CO2 to X products are becoming commercially viable.
Here’s a simple explanation of how the technology works: If you burn any fossil-based hydrocarbon, you get CO2, water, and energy as end products. This new process essentially reverses this combustion reaction: You start with CO2, water, and energy (ideally renewable) and end up with hydrocarbons. As an alternative, CO2 can be reacted with hydrogen (ideally produced from water and renewables via electrolysis) to produce hydrocarbons. The magic happens through a catalyst material—the core IP of virtually every CO2 to X company—that transforms CO2 into a hydrocarbon of choice. The ultimate goals are to use recycled carbon to make synthesis gas or ethylene and propylene, the raw materials in nearly every petrochemical we have today.
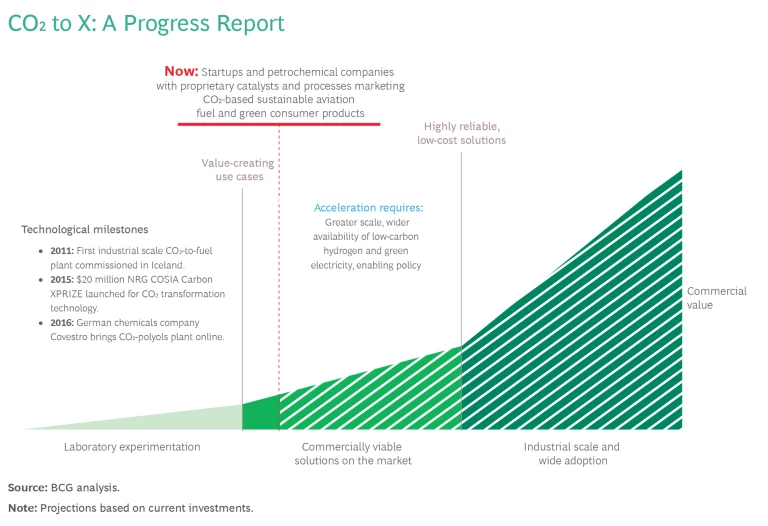
For companies selling high-carbon goods, this technology should be on CEOs’ radar. Recycling and carbon capture won’t be enough: At the end of the day, many customers will want nothing to do with fossil fuels and won’t care how much carbon you sequester. CO2 to X, therefore, will be an important part of many companies’ decarbonization strategies. Even if CEOs approve a new CO2-based project now, however, it may take five to ten years to bring it online at a commercially competitive scale. So it’s time to get started.
Who Are the Players?
The technology to do this on a small scale is already here. Several startups backed by a surge in venture capital over the past five years have products on the market. At this point, most are at the luxury end, targeting consumers willing to pay more to go green. Brooklyn-based Air Company, for example, makes vodka and perfume made from captured carbon. Twelve makes, among other things, lenses for upmarket sunglasses and is developing parts for Mercedes-Benz car interiors. Zara has launched a garment line with polyester made with the CO2 transformation technology of Illinois-based LanzaTech. Perhaps the coolest example: bed mattresses containing polyurethane foam made with Cardyon, a novel material that Germany’s Covestro produces with CO2 recycled from industrial waste.
Several startups backed by a surge in venture capital over the past five years have products on the market.
Other early-stage ventures are pursuing potentially disruptive approaches to converting CO2 into high-value products more efficiently. Germany’s Enadyne, for instance, is using non-thermal plasma process technology to convert CO2 into green chemicals. And US-based startup HYCO1 uses materials science breakthroughs such as a “non-coking” catalyst that is highly efficient at converting CO2 and biomethane or landfill gas to green chemicals, including aviation fuels.
Alternative aviation fuels are particularly hot. In September 2023, the European Commission ruled that at least 6% of fuel supplied at airports in the EU must be made with renewable sources. That mandate will rise to 70% in 2050; half of that renewable fuel is to be “power to liquid,” or PtL, made from CO2, water, and renewable energy. Many of today’s leading CO2 transformation companies, including LanzaTech, Twelve, and Air Company, are now focusing on fuels.
The Road to Industrial Scale
To make a meaningful impact on climate change, the chemicals industry will need to invest in million-tonne-scale production capacity integrated with gigawatts of clean energy. Because CO2 is a very stable molecule, the transformation requires large amounts of energy, ideally from renewable sources. Large-scale production will also require massive amounts of captured carbon.
There’s a strong case to be made, though, that the combination of investment, multiple advancing technologies, and an appetite in the market should drive CO2 to X to a point where it will become price competitive with other options. Unless you are making something like ethylene, most of these chemicals won’t require refineries as massive as today’s integrated petrochemical complexes, which turn crude oil or natural gas into hundreds of chemicals. Instead, the production of chemicals is likely to be distributed close to sources of green energy and captured CO2.
Over the next five years, we expect to see the second investment wave in this technology.
Over the next five years, we expect to see the second investment wave in this technology, as bigger companies acquire the most interesting startups and make much bigger bets, and as momentum from government investment—seen in projects like ARPA-E in the US and Germany’s funding of Evonik’s PlasCO2—increases. Once a foundation of projects is established with several archetype technologies in several locations, we will see the third wave, when the major petrochemical players enter and CO2 to X goes mainstream. This will drive increases in scale and the development of infrastructure for transporting hydrogen and CO2, and it will convince more companies to climb the learning curve—all of which will push down costs.
Companies that start planning now to integrate low-cost, green materials into their supply chains will be at a significant competitive advantage when CO2 to X’s inflection point hits and begins to transform their industries.