The widespread shortage of semiconductors that began in late 2020 highlighted how indispensable these specialized components are in today’s economy. Semiconductors are used to power a vast array of electronic devices—everything from smartphones and cloud servers to modern cars, industrial automation, and critical infrastructure and defense systems.
The global structure of the semiconductor supply chain, developed over the past three decades, has enabled the industry to deliver continual leaps in cost savings and performance enhancements that ultimately made possible the explosion in information technology and digital services. In the past few years, however, several new factors have emerged that could put the successful continuation of this global model at risk. Addressing these vulnerabilities requires a combination of carefully designed actions from policymakers, including targeted incentives to encourage domestic production in order to address strategic gaps.
An Integrated Global Supply Chain
Semiconductors are highly complex products to design and manufacture. No other industry has the same high level of investment in both R&D (22% of annual final semiconductor sales to electronic device makers) and capital expenditure (26%).
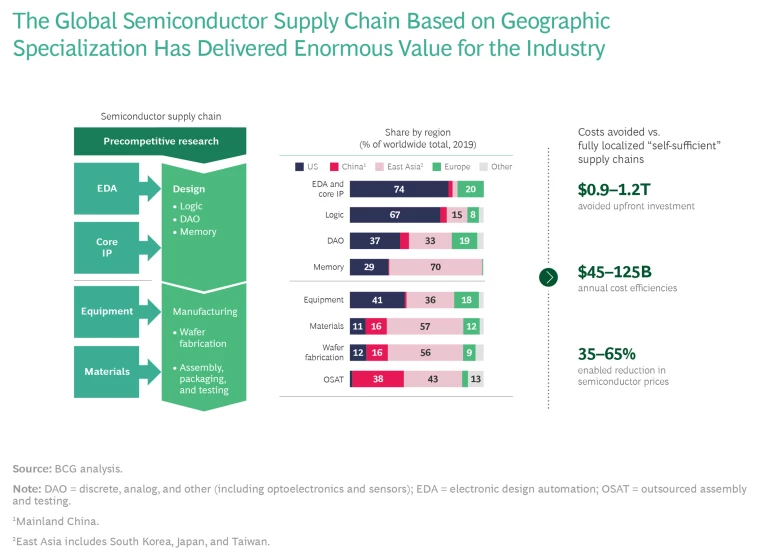
The need for deep technical know-how and scale has resulted in a highly specialized global supply chain, in which regions perform different roles according to their comparative advantages. (See the exhibit.) The US leads in the most R&D-intensive activities—electronic design automation (EDA), core intellectual property (IP), chip design, and advanced manufacturing equipment—owing to its world-class universities, vast pool of engineering talent, and market-driven innovation ecosystem. East Asia is at the forefront in wafer fabrication, which requires massive capital investments supported by government incentives as well as access to robust infrastructure and a skilled workforce. China is a leader in assembly, packaging, and testing, which is relatively less skill- and capital-intensive, and is investing aggressively to expand throughout the value chain.
All countries are interdependent in this integrated global supply chain, relying on free trade to move materials, equipment, IP, and products around the world to the optimal location for performing each activity. In fact, semiconductors are the world’s fourth-most-traded product after only crude oil, refined oil, and cars. This global structure delivers enormous value. A hypothetical alternative with parallel, fully “self-sufficient” local supply chains in each region to meet its current levels of semiconductor consumption would have required at least about $1 trillion in incremental upfront investment, resulting in a 35% to 65% overall increase in semiconductor prices and ultimately higher costs of electronic devices for end users.
Risks and Vulnerabilities
Over the next ten years, the industry will need to invest about $3 trillion just in R&D and capital expenditure globally across the value chain in order to meet the increasing demand for semiconductors. Industry participants and governments must collaborate to continue facilitating worldwide access to markets, technologies, capital, and talent, and make the supply chain more resilient.
While geographic specialization has served the industry well, it also creates vulnerabilities that each region needs to assess in a manner specific to its own economic and security considerations. There are more than 50 points across the supply chain where one region holds over 65% of the global market share, although the level of risk associated with each of these varies. Manufacturing emerges as a major focal point when it comes to the resilience of the global semiconductor supply chain. About 75% of semiconductor manufacturing capacity, as well as many suppliers of key materials—such as silicon wafers, photoresist, and other specialty chemicals—are concentrated in China and East Asia, a region significantly exposed to high seismic activity and geopolitical tensions. Furthermore, all of the world’s most advanced semiconductor manufacturing capacity—in nodes below 10 nanometers—is currently located in South Korea (8%) and Taiwan (92%). These are single points of failure that could be disrupted by natural disasters, infrastructure shutdowns, or international conflicts, and may cause severe interruptions in the supply of chips.
While geographic specialization has served the industry well, it also creates vulnerabilities.
Besides the risks associated with concentration in certain geographic locations, geopolitical tensions may result in export controls that impair access to critical providers of essential technology, tools, and products that are clustered in certain countries. Such controls could also restrict access to important end markets, potentially resulting in a significant loss of scale and compromising the industry’s ability to sustain the current levels of R&D and capital intensity.
The solution to these challenges is not the pursuit of complete self-sufficiency through large-scale national industrial policies with a staggering cost and questionable execution feasibility. Instead, the semiconductor industry needs nuanced, targeted policies that strengthen supply chain resilience and expand open trade while balancing the needs of national security.
To address the risk of major global supply disruptions, governments should enact market-driven incentive programs to achieve a more diversified geographical footprint. This should include building additional manufacturing capacity in the US, as well as expanding the production sites and sources of supply for some critical materials. In our previous report, Government Incentives and US Competitiveness in Semiconductor Manufacturing, we found that a $50 billion incentive program would establish the US as an attractive location for semiconductor manufacturing. Our analysis shows that such a program could enable the construction of 19 advanced fabs for logic, memory, and analog semiconductors over the next ten years, doubling the number expected if no action is taken.
Subscribe to receive the latest insights on Technology, Media, and Telecommunications.
This new capacity would be instrumental to address major vulnerabilities in the supply chain. For example, it would allow the US to maintain a minimum viable manufacturing capacity in the leading nodes to meet domestic demand for the advanced logic chips used in national security systems, aerospace, and critical infrastructure. In contrast, we estimate that a goal of complete manufacturing self-sufficiency—seeking to cover the total US semiconductor consumption with onshore capacity—would require over $400 billion in government incentives and cost more than $1 trillion over ten years.
In setting policies to promote supply chain resilience, governments must guarantee a level global playing field for domestic and foreign firms alike, as well as strong protection of IP rights. They must also take steps to further promote global trade and international collaboration on R&D and technology standards. In parallel, policymakers need to step up efforts to stimulate basic research and address the shortage of talent threatening to constrain the industry’s ability to maintain its innovation pace. To that end, further public investment in science and engineering education is needed, as well as immigration policies that enable leading global semiconductor clusters to attract world-class talent.
Targeted government action is needed to foster investments that diversify the global manufacturing footprint and sources of supply for key materials.
In addition, governments with significant national security concerns should establish a clear and stable framework for targeted controls on semiconductor trade that avoid broad unilateral restrictions on technologies and vendors.
Such well-modulated policy interventions would preserve the benefits of scale and specialization in today’s global supply chain structure. This would ensure that the industry can extend its ability to deliver the continual improvements in semiconductor performance and cost that will make the promise of transformative technologies such as AI, 5G, IoT, and autonomous electric vehicles a reality in this decade.
This report would not have been possible without the contributions of our BCG colleagues Anoop Shah, Zhenyu Bo, Kaitlyn Alsup, Sohini Kar, and Yeonsoo Lee.