Compared with many other sectors, industrial machinery’s digital transformation has hardly been swift. To be sure, suppliers of everything from manufacturing equipment to tractors have begun the journey. They’re embedding digital technologies and connectivity into their hardware and mining data to predict maintenance needs, deliver value-added services to customers, and equip factories of the future.
But thus far, most machinery and industrial-automation OEMs are achieving only incremental advances from their digital endeavors—not blockbuster leaps. And they’re behind the curve when it comes to full digital transformations that span their operating models, processes, technology platforms, ways of working, and customer engagement. For these reasons, the digital initiatives of most industrial goods companies have yet to fully translate into superior financial performance.
To gauge their digital progress, we took an in-depth look at dozens of machinery and industrial- automation companies around the world. At first glance, we saw little direct correlation between digital sophistication and revenue and profit margin growth. But when we dug deeper, interesting patterns emerged. We found that machinery makers with the strongest financial performance are far better at executing their digital vision and strategies. They are especially more advanced in creating digitally empowered services and solutions and implementing agile ways of working. They’re also much stronger in digital innovation, successful lighthouse and rapid prototyping projects, creation of new digital businesses, and customer-centric business models. Many financial underperformers, by contrast, fail to get their digital ambitions into execution mode.
These findings highlight the capabilities where underperforming machinery and industrial-automation companies should target their investments in order to close the gap with market leaders—and where high performers can focus to become even stronger.
Assessing Digital Maturity
We interviewed executives at 81 machinery and industrial-automation companies in the US, Europe, Japan, and China in six industry segments: automation components, general-purpose equipment, mechanical components, off-highway vehicles and mobile machinery, industrial plants, and stationary and shop floor machinery. We assessed 53 digital-maturity checkpoints for each company and generated scores based on BCG’s
Digital Acceleration Index
(DAI), which identifies where companies lag and where they have a competitive edge. We grouped the surveyed companies into four categories:
- “Starters” have DAI scores between zero and 25. Their organizations are not yet digitally enabled and tend to lack a clear digital vision. Starters typically address digital topics based on ad hoc demands.
- “Literates” score from 26 to 50 on the index. They have a clear digital strategy and are optimizing their processes. Governance is often digitally enabled. But while literates are executing digital initiatives, businesses and functions still tend to operate in silos.
- “Performers” have DAI scores between 51 and 75. They have a strong digital mindset, an agile culture, and digital capabilities across all areas. They successfully build and commercialize digital initiatives and, in some cases, have launched disruptive business models.
- “Leaders” have DAI scores from 76 to 100. Digital initiatives are clearly contributing to strategy and adding value. Digital is embedded throughout the organization and is a key element in innovation, the company’s value proposition, technology, and operations.
Overall, the industrial-machinery sector is at the literate stage of its digital journey. (See Exhibit 1.) It’s well behind sectors such as consumer goods, finance, and health care, and even lags the public sector. In terms of market segments, only automation components and off-highway vehicles are at the cusp of performer status; industrial plants and stationary machinery are barely past the starter stage. This is more or less true regardless of region: although European machinery companies post higher DAI scores on average than those of China, Japan, and the US, they still rank only as literates.
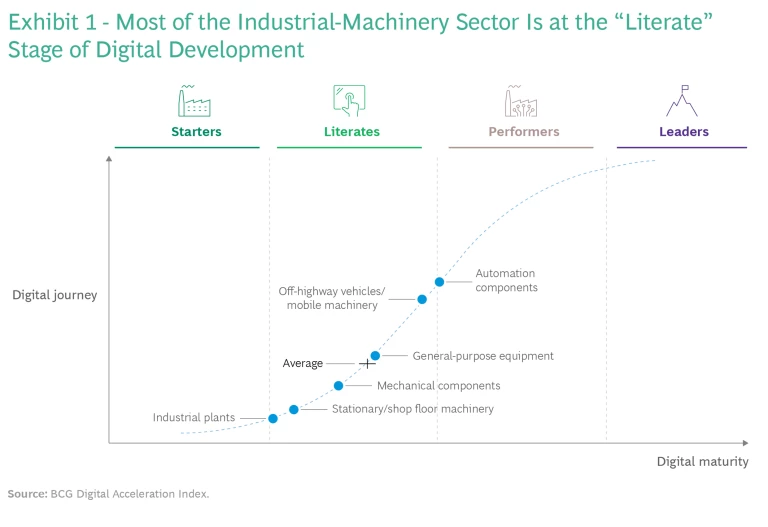
We found that machinery companies in the vanguard of digital adoption are much more successful at executing their digital strategies. Machinery companies with DAI scores of 60 or higher (which we call “champions”) far outpace laggards (those with scores of 35 or lower) on eight key building blocks that relate to operations. These building blocks include “purpose and strategy”—a company’s overarching goals—as well as digital capabilities, talent, and work environment.
We refer to the difference between a company’s DAI score on purpose and strategy and its scores on the other seven operational building blocks as the digital execution gap. For champions, this gap is only around 7%, on average. But for laggards, it averages 55%. (See Exhibit 2.)
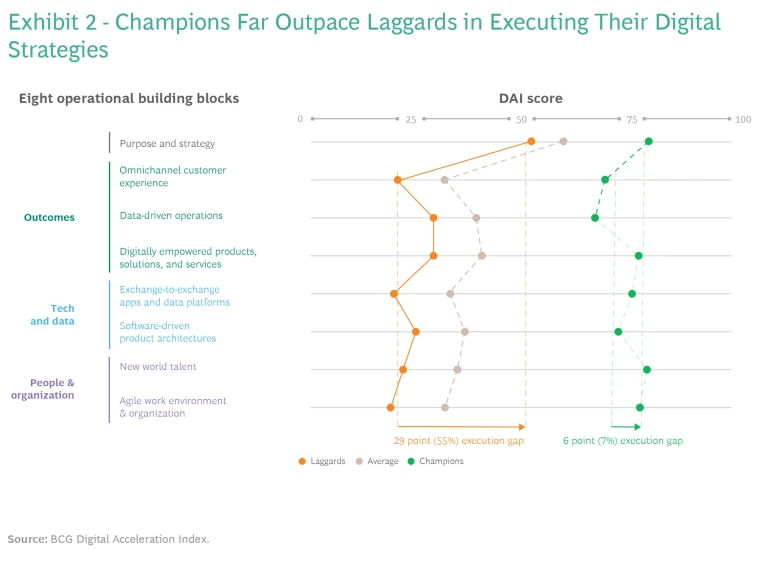
Linking Digital Prowess to Financial Performance
To determine whether there is any correlation between digitization and long-term market success, we analyzed financial indicators for each company, including revenue and profit growth over the past five years. We found little direct correlation between digital leadership and superior revenue and profit margin growth. This finding held true regardless of market segment or region.
The picture was different, however, when we compared machinery companies with the best financial results over the past five years and those with the weakest. We identified 15 financial high performers, companies whose compound annual growth in both revenue and EBIT margin was at least 2 percentage points above the average for the entire industrial-machinery sector. These high performers averaged annual growth of 6% in revenue and 9% in earnings over those five years. At the other extreme, 10 financial underperformers posted annual growth of –2% in revenue and –10% in earnings over the same period.
The financial high performers averaged DAI scores of 43, while the underperformers averaged 33. This difference is significant enough to suggest a link between digital sophistication and financial results over time.
The contrast between high performers and underperformers grew sharper when we examined DAI scores on specific digital checkpoints. Eight checkpoints in particular stood out as making a difference in financial performance. We identified four of them as key “differentiators” of digital success: service operations, prototype and lighthouse projects that serve as models, innovation power, and the building of new businesses. In addition, we found that pricing and artificial intelligence are key “enablers” of digital success. Finally, digital talent and customer centricity are cross-organizational cultural factors.
Subscribe to our Industrial Goods E-Alert.
Our analyses revealed significant differences between the DAI scores of financial high performers and underperformers on each of these digital checkpoints. (See Exhibit 3.) Some of the largest gaps—of more than 20 points—were in innovation power and new-business creation. High performers ranked as literates only in pricing and AI, however, suggesting that even the most digitally sophisticated machinery companies are struggling to make their digital offerings available at the right prices for customers. (As they become more sophisticated in AI, these companies should be able to adjust their prices to take into account such factors as geography, the level of competition, and technological differentiation.) Still, financial high performers are ahead of underperformers, which remain at the starter stage in pricing and AI. High performers also had good scores in the cultural differentiators of digital talent and customer centricity, although the gaps with underachievers were a bit smaller.
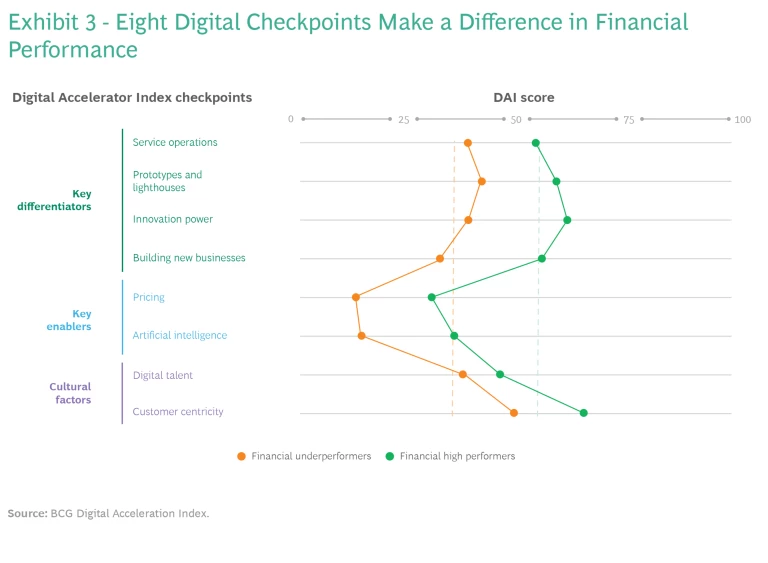
How Financial Performers Are Leveraging Digital
Several leading machinery companies illustrate the advantage of being a high financial performer as well as digitally mature. A number of them, for example, have introduced digitally empowered products:
- A leading manufacturer of agricultural machinery with EBIT margins of 18% in 2021 has developed an IT system that draws on real-time machinery, soil, weather, and other data to help farmers make more informed decisions about seeds and fertilizers, when to plant, and how to manage their equipment.
- A designer of engineering software, which averaged 21.5% EBIT margins and 9.7% annual revenue growth from 2016 through 2021, has combined its legacy product life cycle management system and computer-aided design software into next-generation simulation and digital-twin solutions that result in a more integrated customer experience.
- A major maker of power tools, whose EBIT margins averaged 12.6% from 2016 through 2021, has embedded digital technologies and connectivity into many of its products to make them safer and more reliable. In addition, it has established R&D hubs around the world and a partnership with a startup accelerator that focuses on AI in advanced manufacturing.
- An automation equipment OEM with consistent revenue and profit growth of 8% and 9%, respectively, over the past five years has established global R&D hubs focused on expansion into areas such as quantum computing and automated driving.
- A leading robot OEM with EBIT margins consistently greater than 15% has linked its services hotline, spare parts logistics, and field services to expedite service and spare parts availability. It has also launched an augmented-reality app that has reduced the average time between customer service calls and repair completion to 28 hours.
The Keys to Translating Digital into Financial Success
Machinery and industrial-automation companies can start improving their financial performance by focusing on the following:
- Core Service Operations. Rather than selectively supporting certain operations with legacy tools, machinery companies should adopt an integrated approach that leverages data analytics and automated workflows.
- Lighthouse Projects and Prototypes. The development process for new digital offerings should shift to releasing new goods and services quickly. Rather than iterating on a new design for five years or so until the product is “perfect”—only to see it fail in the marketplace—companies should rapidly generate prototypes based on continuous, incremental improvements that are tested early with customers, allowing flawed iterations to fail early.
- Innovation Power. Rather than improving established goods and services, innovation activity should focus on using digital technologies to redefine existing product portfolios and create disruptive new offerings.
- New-Business Development. Shift from enhancing products and businesses with digital features to systematically launching new corporate ventures based on a clearly articulated strategy and methodology.
- Pricing. Industrial-machinery companies should use CRM tools and analysis of market intelligence data to identify the “right” price, taking into account the market value of their equipment and solutions.
- Artificial Intelligence. AI should be seen as a key driver of value creation. Use cases should be identified across the organization, spanning product development, procurement, sales, and customer service.
- Digital Talent. As they add experts with advanced IT and AI skills, companies should adopt new ways of working that are common in the digital world. These practices—which can coexist with traditional ways of working—include flexible hours, remote collaboration, and an agile approach to innovation.
- Customer Centricity. New digital offerings should be driven by a clear understanding of customer needs. Departments throughout the company should collaborate in collecting feedback and testing initiatives.
A Digitization Approach for Industrial Machinery
Our benchmarking of the machinery and industrial-automation sector’s
digital maturity
in relation to other industries indicates that there are many unmet opportunities for digitization. Companies can begin to tackle the process by doing the following:
- Adopt an approach to innovation that accelerates time to market. This means rapid prototyping and testing with the client and aiming for blockbuster disruption, as opposed to incremental progress. In some cases, it will necessitate the rethinking of entire business models.
- Review the organization’s support and service operation. Automation, data collection, and linked processes will improve efficiency and profits. Modern robotic process automation, for example, can work miracles, even within a legacy IT system.
- Start leveraging AI today so that it can immediately impact the bottom line. There is no second-mover advantage in adopting AI. In the machinery sector, this is especially true when it comes to price. But many other use cases across the value chain can also benefit from AI, such as R&D, procurement, and service offerings.
- Begin a cultural transformation, which is a must for attracting and retaining the right people. This doesn’t mean that successful teams must be forced into a new working model. Agile teams can coexist with teams working under the traditional model. Customer centricity, however, should be the lifeblood of all teams.
A full digital transformation is a multiyear journey that usually requires holistic change across the organization before it produces dramatic results. Beginning that journey now can not only start improving financial performance immediately but secure competitive advantage well into the future.