Given the proliferation of apps, platforms, and advanced technologies available to manufacturers, it is not surprising that many shop floors are filled with a wide array of tools designed to enhance the productivity of frontline workers. The problem, in many cases, is that these tools have been designed independent of feedback from these same workers: the tools are, in effect, designed for them, but not with them in mind. As a result, workers tend to either ignore the tools or use them only sporadically and the tools fail to deliver the productivity benefit it was supposed to deliver.
To make tools that frontline workers want to use—tools that actually benefit both the workers and the company as a whole—the tools must be sticky, and that involves putting frontline workers at the center of the design process.
Poor design leads to digital overload
In our work with clients, BCG X’s Manufacturing AI team has observed several ways in which poorly designed shop floor tools fail to deliver for frontline workers — and the manufacturing process itself. It begins with something as simple as a worker’s inability to easily access a tool. This can be a result of simple operational realities/circumstances such as lack of WIFI access, or onerous login details.
The experience can then be compounded by systems that entail multiple tools and/or screens with multiple logins, disconnected systems that require workers to input the same information numerous times. Furthermore, often third-party data ownership blocks the company’s ability to use advanced analytics to drive further productivity benefits. Unnecessarily complex tool design, lack of consistent, user-friendly interfaces and confusing or imprecise language that can lead to incorrect or inconsistent data capture. Most critically, poorly designed systems that fail to deliver significant and timely perceived value to frontline workers often end up not being used— tools that require workers to take time to input an inordinate amount of data without delivering any discernable benefit. A solution to these problems is simply to make sure the workers themselves play a role in how these tools are designed.
Five principles for creating sticky digital tools
Shop floor tools that frontline workers will use are those that make their work lives easier—that enable them to escalate problems easily, that make their equipment more reliable, and their work weeks more predictable, and that boost their productivity. In our experience, we have found five principles that lead to these kinds of sticky tools.
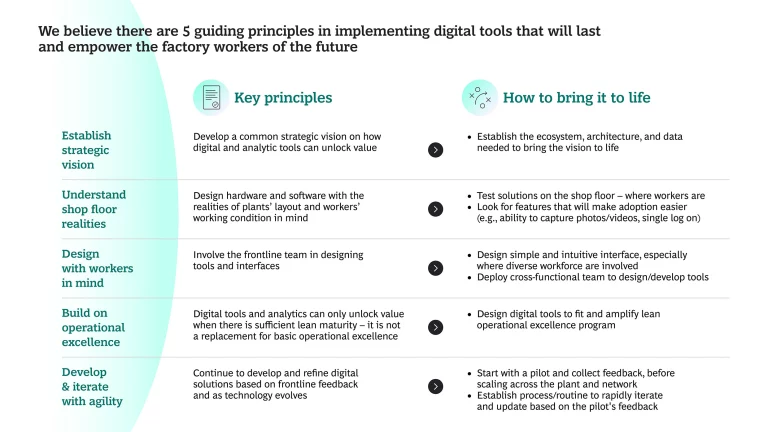
Build on operational excellence: Organizations that introduce digital and analytic tools without getting the ‘basic’ operational excellence in place often fail to realize the full value the tool brings. We believe that having an operational excellence program in place is foundational and digital tools should amplify those programs and accelerate value delivery.
Understand shop-floor realities: This may seem obvious, but design teams need to spend time on the shop floor. What are the realities of the manufacturing process, as experienced by the front-line workers? What language are the workers most comfortable using? How is the manufacturing process laid out? Which digital applications do frontline workers use on the shop floor (e.g. if they use Microsoft Teams, then recommend using Teams for messaging). Observe the shop floor closely to understand the operational reality of the people doing the work.
Design with workers in mind: Similar to but not the same as the workers’ preferred language, understand the language that resonate with them. What terms do they themselves use to describe the processes, the machinery, the milestones, the fail points? How big on the screen do words and icons need to be? What is the fewest number of screen prompts the workers follow to log the required information? How easy is it for workers to provide real-time feedback?
Manufacturing equipment often comes with a built-in suite of digital tools. These tools are typically designed to help optimize the equipment based on operational needs, often prioritizing the goals of engineers or managers rather than the day-to-day realities of frontline workers. For instance, they may require workers to follow lengthy processes at the end of their shifts, just when they are ready to go home, or may require the worker to move across different parts of the plant to input data. Such systems are anything but ‘sticky’ as they discourage consistent use and frustrate rather than empower the worker.
Establish your strategic vision: Think broadly to create an ecosystem in which other apps or tool applications can be quickly scaled. Before you design a new shop floor app, for example, make sure that the platform you are building it on is scalable. You might go with one of the established cloud service providers. Or you could decide to build your own custom platform. Whatever you choose, make sure your cloud platform provider is robust enough to handle what may become a rapidly expanding data infrastructure.
Develop and iterate with agility: Building digital tools capable of capturing the subtleties of complex manufacturing processes is difficult to do the first time around. Instead, capture feedback from the shop floor
workers and then iterate. We have found that workers are willing to take the time to provide feedback as long as they see personal benefit in doing so, whether measured by improvements in productivity, reductions in equipment downtime, or greater job satisfaction.
Part of this iterative design process should be observing the workers on the shop floor, shadowing them to see how they use the tool. You might ask them, for instance, how they would sequence a series of steps, and then observe them as they perform the steps their way to see if and how it changes the outcome.
Delivering tangible benefits
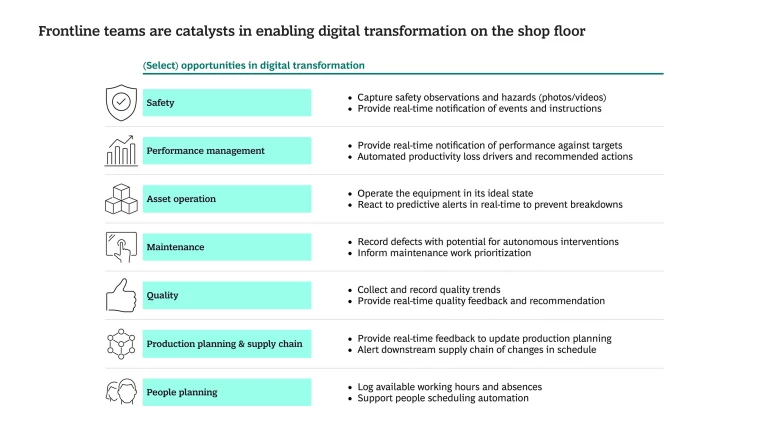
There are numerous, significant advantages to creating shopfloor tools that frontline workers actually use. Safety hazards can be quickly flagged, with real-time notifications sent up the chain. Maintenance logs can be created to capture and monitor potential hazards. If machine output falls below target, the worker can immediately diagnose the root cause.
Furthermore, good digital tools can provide technicians with immediate access to the steps necessary to correct problems, rather than them having to search through long text documents. In a well-designed system, these steps can be served up on a portable screen, complete with AI agents to help the technicians implement and trouble shoot the steps in real time. AI can also be leveraged to customize screen language to the individual user’s preference with the click of a button.
For many highly technical manufacturing lines, one of the key elements of productivity is having the right worker with the right skills available at the right time. Digital tools with planning logs provide line supervisors with a high degree of transparency into shift planning to ensure that production lines continue without interruption.
Producing tangible results
In its work with 1,200 manufacturing clients over the past five years,
Manufacturing AI by BCG X
has deployed both traditional lean and digital tools with shop floor workers. As a result, we have front ends powered by advanced analytics and tailored for manufacturing users, along with customizable back-end modules ready to be deployed on proprietary BCG platforms or client/partner environments of choice. Client results thus far include 10-15% improvements in productivity, 10-15% reduction in conversion costs, and 60-80% increase in internal rate of return.