By 2030, the severe semiconductor shortage now hobbling much of the world’s automobile industry will hopefully be a distant memory. But by that time, a shortage of another critical material—lithium—is forecast to be hitting in full force.
Lithium is a powdery white metal used in the vast majority of rechargeable batteries that power electric vehicles (EVs) and that store electricity generated through renewable resources. This looming supply crunch, if not addressed through coordinated action, could significantly set back the transition from fossil fuels to renewable energy and the global battle against climate change.
The race is on around the world to secure future sources of lithium and diversify supply chains. Leading battery manufacturers and automakers are competing to strike long-term contracts with miners and refiners. Countries with large auto industries are trying to develop their own regional lithium-ion battery supply chains, a trend that will accelerate with recent passage of the Inflation Reduction Act in the US. And nations with reserves of lithium and other critical battery materials, such as nickel, are using them as leverage to build domestic battery industries.
The challenge is how to address the potential lithium crisis in an environmentally and economically sustainable way. That will require collaboration among all players in the value chain. Mining companies, refiners, battery manufacturers, automotive OEMs, and financiers should work together with governments, NGOs, and other stakeholders to ensure that lithium-based battery projects adhere to best environmental practices and deliver a fair share of benefits to nations and local communities. International partners should also provide the technology, expertise, and market access needed for national and local battery-related projects to become commercially viable.
Why Lithium Is So Critical
The improved performance and falling cost of lithium-ion batteries over the past decade have been a major force driving the adoption of electric cars and trucks. The expectation that these trends will continue is a big reason why BCG forecasts that vehicles powered purely by electric batteries will surpass those with gasoline-powered internal combustion engines as the most popular type of light vehicle sold globally by 2028. By 2035, BCG projects that 59% of all light vehicles sold globally will be battery-electric vehicles (BEVs).
The race is on around the world to secure future sources of lithium and diversify supply chains.
Lithium-ion batteries are also used for 90% of grid energy storage around the world, especially for wind and solar energy. Initiatives such as the EU’s plan to reduce its dependence on Russian natural gas by two-thirds, which relies in part on accelerated generation of renewable energy, will significantly increase demand for battery storage.
A number of other minerals, such as nickel, manganese, and cobalt, are also important ingredients in various types of lithium-ion batteries. But lithium is the most critical. It’s used to make cathodes, an essential component of every type of lithium-ion battery. It’s also likely to be required in the high-capacity anodes of the future. In addition, lithium is used in the electrolyte solutions that allow ions to travel between the cathode and anode inside batteries, allowing them to store energy and deliver power.
Of course, alternatives to lithium-ion batteries as storage options for vehicles and power grids are in development. For the foreseeable future, however, none of these will offer the combination of cost, weight, and volumetric energy density of lithium-ion batteries. Nor is their production reaching the scale needed for the massive volumes that will be required.
The Lithium Supply Challenge
The supply crunch won’t hit immediately. Even though the price of lithium has surged more than tenfold over the past two years, there’s enough capacity to meet anticipated demand until around 2025—and potentially through 2030 if enough recycling operations come online. After that, chronic shortages are expected. Even assuming that all the new lithium-mining projects that the industry currently regards as probable or possible go into operation, as well as a significant expansion of lithium-recycling projects, lithium supply in 2030 is expected to fall around 4% short of projected demand, or by around 100,000 metric tons of lithium carbonate equivalent (the processed form of raw lithium). (See Exhibit 1.) By 2035, that supply gap is projected to be acute—at least 1.1 million metric tons, or 24% less than demand.
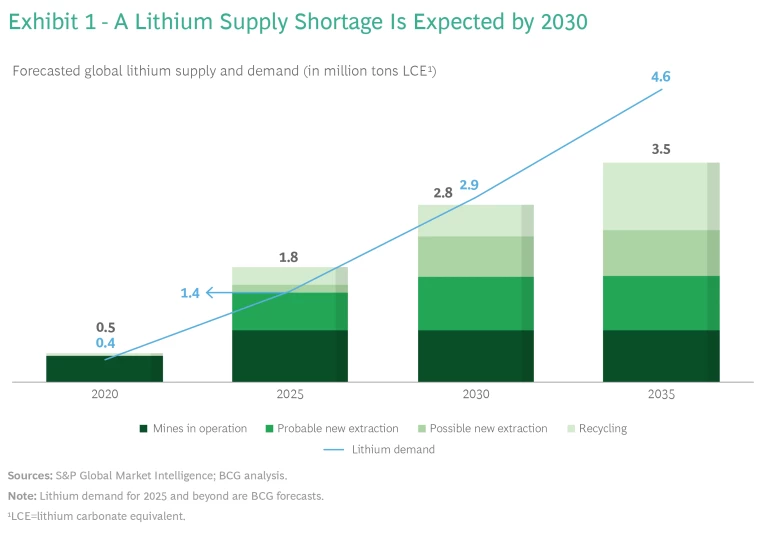
Two factors are behind the expected shortfall. First, the amount of lithium extracted from deposits around the world is projected to fall well short of demand. Second, the capacity for refining the mineral into the chemicals used in lithium-ion batteries is heavily concentrated in a handful of countries. Major disruptions, whether due to geopolitical events, natural disasters, or another pandemic, could put the entire battery supply chain at risk.
Dramatically increasing production will be challenging. One reason is that conventional lithium mining can pose a number of environmental hazards, such as soil and groundwater contamination. The technologies and processes currently used in lithium extraction require vast amounts of water, a serious drawback in arid regions. As a result, mining projects have faced opposition on environmental grounds in countries such as Portugal, Serbia, and the US. And while the discovery of large new lithium deposits could change the supply dynamics, environmental issues would still likely have to be addressed.
As explained below, new extraction methods and technologies are under development that hold promise for reducing the environmental impact of lithium extraction. The challenge is to deploy such techniques at scale.
Supply Chain Vulnerabilities
The concentration of key parts of the supply chain in very few countries represents a further risk to a future powered by lithium-ion batteries. (For a description of the supply chain, see Exhibit 2.) Most of the refining of lithium into the chemicals used to make battery components is done in two countries. Chile exports 66% of the world’s supply of lithium carbonate, which it extracts from evaporated saltwater brine. China produces most of the rest using a different method—refining the lithium carbonate from spodumene ore, primarily sourced from Australia. Lithium carbonate is used in electrolytes and is also refined into lithium hydroxide, a critical ingredient in cathodes. China accounts for more than half of global lithium hydroxide exports.

China is also the world’s leading producer of cathodes, battery cells, and battery packs, both for its domestic EV industry and for export. Japan and South Korea, too, are major exporters of battery packs.
In addition to the strategic risks stemming from the concentration in so few places of so much of the supply of critical materials, the logistics of the current global supply chain are very inefficient. Because of their weight, lithium-ion batteries are increasingly manufactured close to EV assembly plants. This means that huge volumes of ore or lithium carbonate are shipped long distances to China for refining and are then shipped back across oceans in the form of lithium hydroxide or cathodes to nations that manufacture battery cells and packs. Diversifying global sources of critical materials would not only make supply chains more resilient, but would also reduce the costs and carbon emissions associated with shipping.
Every major automotive OEM is scrambling to secure future sources of critical lithium materials. Tesla, for example, has signed a three-year agreement with China’s Ganfeng, one of the world’s largest producers of lithium compounds. Volkswagen is seeking to create what former CEO Herbert Diess has called a “full ecosystem of suppliers from lithium extraction to the assembly of batteries” in Spain; the company has also entered into an agreement with the German-Australian company Vulcan Energy Resources to obtain lithium from Germany’s Upper Rhine Valley region. Vulcan, meanwhile, has made preliminary supply agreements with Renault and Stellantis. Ford has agreed to buy 25,000 metric tons of lithium annually from the Argentina facility of Australia-based Lake Resources.
The Race to Develop Domestic Supply Chains
The recently passed Inflation Reduction Act in the US illustrates another global trend reshaping the battery industry—a race to create domestic, vertically integrated battery industries with locally produced critical materials. The US legislation provides incentives of up to $7,500 for the purchase of new EVs built in the US, Canada, or Mexico. But the offer comes with stringent local-content requirements. To qualify for half the incentive amount, EVs must eventually contain battery packs assembled in North America. To qualify for the other half, a certain portion of the critical minerals used in the batteries must come from nations with which the US has free-trade agreements. This requirement will be phased in and reach 80% in 2029. In addition, vehicles whose critical-minerals supply chain flows through “foreign entities of concern” will be disqualified from receiving this half of the incentive amount.
In the European Union, meanwhile, the European Battery Alliance, funded by the EU Commission, has taken several steps to secure lithium and other minerals critical to the energy transition. And in India, before approving and awarding incentives to proposed battery projects, the federal government requires assurances that they will meet certain thresholds for local content.
By 2035, the lithium supply gap is projected to be acute—at least 1.1 million metric tons, or 24% less than demand.
At the same time, nations with critical raw materials are seeking to leverage their reserves to build domestic battery industries. Indonesia, for example, supplies one-third of the world’s refined nickel. It wants to deploy new processes, such as high-pressure acid leaching, to refine more nickel into battery-grade metal. Indonesia also wants to develop downstream manufacturing. A consortium of state enterprises, including a mining company that owns a significant share of the nation's nickel reserves, has signed a memorandum of understanding with LG Energy Solution to invest in a $9 billion consortium to process the metal and manufacture cathode materials, cells, and finished batteries. It has also signed an MOU with China’s Contemporary Amperex Technology (CATL), which has announced plans to invest in a $6 billion initiative with Indonesian partners to develop battery manufacturing, recycling facilities, and mining projects.
It’s natural that nations with large lithium reserves will want a greater share of the economic wealth generated by the rechargeable-battery boom. The mining, initial processing, and refining of lithium account for 25% to 30% of the available profit pool for lithium-ion batteries. The manufacture of anodes, cathodes, and electrolytes accounts for a 20% to 25% share. Production of cells and assembled batteries represents 45% to 50% of the batteries' profit pool.
Addressing Environmental Risks
Before new lithium-mining operations can be brought online, the environmental hazards of mining must be addressed. Governments and stakeholders need to weigh the tradeoffs between mining’s impact on local environments and the benefits of a net reduction in CO2 emissions from vehicles.
New mining projects must be environmentally sustainable in order to compete in the face of stiffening regulations in global markets. Starting in 2024, for example, the EU will require importers to declare the CO2 footprints of batteries sold in the region. The EU will also set emission limits and require that a certain amount of lithium be recycled. In addition, the European Commission is considering establishing a “battery passport,” a technology platform that will enable everyone in the supply chain to share information on the manufacturing history of every battery sold in the EU.
Process innovations could make lithium extraction much more eco-friendly. Some new technologies and mining best practices hold promise for reducing the environmental impact to a level consistent with the highest environmental standards, such as those of the EU. For example, direct lithium extraction (DLE), in which most brine water is recycled, could greatly reduce the amount of water required.
Several pilot projects are underway to use DLE to recover lithium from naturally occurring geothermal brine deposits. Geothermal energy is used to extract the lithium, and the brine is then recycled back into the geothermal source. Vulcan Energy Resources and Cornish Lithium of the UK are among the companies investing in geothermal brine projects.
Featured Insights: BCG’s most inspiring thought leadership on issues shaping the future of business and society
A Framework for Sustainable Lithium Development
Companies across the battery value chain must mobilize now to boost supplies and diversify their supply chains. Economic development and geopolitical pressures are creating the need for integrated, regional battery industries. In many cases, mining companies, refiners, battery manufacturers, and automotive OEMs will need to revamp their global manufacturing and sourcing footprints in order to bring more output closer to markets where EVs are sold. The US Inflation Reduction Act is set to kick off the next wave of capacity investments, supply chain reshuffling, and product portfolio adjustments. Other governments are likely to make moves in response.
To accomplish this mobilization and protect supplies, coalitions are needed. Miners, battery manufacturers, automakers, governments, and financiers must work together to ensure that desperately needed lithium extraction projects migrate from the possible to the probable category in terms of their likelihood of coming online. To be successful, extraction projects should apply a framework for success that includes the following actions:
- Bring best practices in environmental sustainability. International mining and manufacturing partners should bring state-of-the-art technologies and processes such as DLE to minimize water and soil contamination and reliance on fossil fuels. Global partners can help domestic companies implement systems for documenting and reporting their carbon footprints to comply with increasingly stringent regulations in key global markets.
- Create opportunities to develop downstream industries. International partners should work with governments to bring downstream industries closer to lithium reserves and make them part of regional supply chains. Mining companies, processors, and manufacturers of batteries and key components can provide advanced production processes, operating expertise, and access to international markets. Automotive OEMs can support local battery industries by committing to purchase large volumes of output on long-term contracts. Investors, such as financial institutions, sovereign funds, and private equity firms, can provide stable financing to build industrial capacity.
- Guarantee fair value for domestic stakeholders. To ensure that host governments and local communities benefit adequately from their natural resources, royalties, shares of profits, and other benefits should be substantial enough to secure popular support for the long term. International investors in battery projects can also contribute to broader economic development and industrial capabilities by investing in infrastructure, skills-training programs, and partnerships with education systems. National and municipal governments can provide financial support and other incentives and work with international consortia to ensure that projects help advance economic and social goals.
Meeting the explosive growth in demand for lithium products in the coming years poses a host of daunting challenges. But these challenges must be met if the transition to renewable energy and the global fight against climate change are to stay on course. We believe that public-private coalitions across the rechargeable-battery value chain can not only meet industry’s needs for critical materials. They can also develop these resources in ways that are environmentally sustainable, advance the economic development agendas of governments, meet key localization requirements, and deliver a fair share of benefits for local communities.