Heavy industries like mining and agriculture are making ambitious commitments to reduce their greenhouse gas emissions. But the diesel truck fleets these companies use—everything from 300-ton haulers at mining sites to18-wheel tractor trailers on highways—are a primary source of CO2. These vehicles all burn diesel, making up a large share of the industries’ overall environmental footprint. Unless companies commit to eliminating or reducing diesel fuel, they simply won’t hit their net-zero targets.
We recently analyzed alternative fuels to determine how they could perform in a range of trucks and applications. The key takeaway? It’s not easy to displace diesel in transportation and logistics or in other industries requiring heavy equipment, but it is possible, through two broad options that companies can apply individually or together:
- Speed and Ease—but at a Cost. Companies that want to make a change today can implement a straightforward switch to sustainable biodiesel using the same vehicle fleets and infrastructure, provided they are willing to pay higher fuel costs.
- Lower Cost but Greater Complexity and Time Requirements. Companies that want to keep costs low can eliminate diesel, but the process will take longer, be more complex, and rely on new technology for alternative fuels, infrastructure, and vehicles.
A global mining company weighed these two options for its fleet and proactively engaged with its OEM and energy suppliers to understand which technologies were technically feasible and commercially viable. It determined that it could remove more than 6 megatons of CO2 per year, 20 years earlier than planned—equal to eliminating nearly 1.5 million passenger cars.
Companies don’t have to wait until 2050 to eliminate diesel. In fact, if they are serious about combating climate change, they can’t wait.
Why Diesel Is Hard to Replace
Diesel is widely used in heavy industries for good reason: it’s cheap, energy dense, and readily available through established infrastructure. Different applications and industries have individualized operational requirements—variable payloads and distances, whether they’re used on or off roads—but diesel is a universally applicable fuel.
Because it is relied on across so many industries, diesel combustion represents a huge share of overall emissions, comprising up to 40% of all CO2 emissions for mining and 35% for agriculture. Moreover, replacing diesel is challenging, requiring a systems-level approach that includes not just different types of fuel but also new powertrains and onboard fuel systems. Companies must also consider all the fuel infrastructure—like pipelines, storage tanks, and refueling and recharging stations—that will need to be upgraded.
Fortunately, several diesel alternatives exist already, and others are under development. Each presents tradeoffs for fleet operators, but the benefits can be striking. In particular, there are four alternatives that companies should consider. (See the exhibit.)
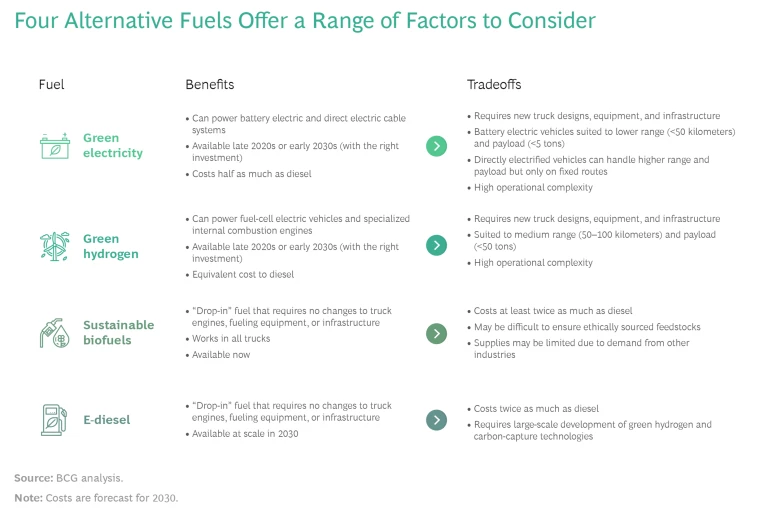
Green Electricity. One potential fuel source is energy derived from renewable sources such as wind and solar. Green electricity can be used directly or utilized to power the industrial processes required to generate other alternative fuels. Battery electric power generated from renewable sources is viable for privately owned passenger cars, which often sit unused for a portion of a given day. They are therefore easy to charge and don’t operate at anywhere near their payload limit (meaning heavy batteries aren’t an issue). By contrast, the weight of the battery and recharging time needed for heavy equipment and vehicles—and their need to operate close to their maximum payload and operate for long periods between recharging—makes battery electric power a more challenging option.
Some workarounds offer niche solutions. For example, heavy vehicles that operate on highly predictable routes—such as deep-pit mining trucks—can be powered through overhead electrical cables that remain in direct contact with the vehicle, similar to the light-rail systems used in some cities. Where it works, this is a great solution. However, it won’t work everywhere or for all vehicles, and installing the power lines requires additional capital investment.
Green Hydrogen. Hydrogen can be produced using water as a feedstock through an industrial process known as electrolysis. If that process is powered by renewable energy sources such as wind or solar, the result is carbon-neutral (“green”) hydrogen, which can be burned in specialized internal combustion engines or used to power hydrogen fuel cells. Fuel cell passenger vehicles are available today and provide longer ranges and faster refueling than electric vehicles, making them a preferred solution for long-haul trucking on highways. However, hydrogen is significantly less energy dense than sustainable biofuels and e-diesel (which means that it requires a larger fuel tank and longer refueling times than diesel) and therefore presents challenges for vehicles or equipment where productivity and payload matter.
Sustainable Biofuels. A range of sustainable biofuels are entering the market, including hydrotreated vegetable oil (HVO), which is produced by processing waste vegetable oils or animal fats, and green diesel, which is produced by processing biomass waste such as crop residues, wood, and sawdust. Both can replace diesel in current fleets without requiring changes to engines or storage infrastructure, but they are currently far more expensive than diesel. They can, however, reduce emissions by up to 90%. (They do not fully eliminate emissions because they still require some energy to produce, but the bulk of their carbon footprint has already been accounted for in other industry lifecycles.)
In addition to cost, sustainable biofuels present two challenges. The first is the importance of ensuring that feedstocks are ethically sourced (to maintain a sustainable and net-positive outcome), although some systems are emerging to provide “traceability” guarantees to end users. The second is supply. Production is forecast to reach 570 million barrels by 2030, but that only accounts for a small proportion of the diesel consumed in mining, agriculture, and road freight. What’s more, other hard-to-abate industries increasingly compete for the same feedstock that is used for HVO (such as the aviation industry’s growing demand for sustainable fuel), so supplies will almost certainly be constrained.
E-diesel. A carbon-neutral synthetic form of diesel, e-diesel can be produced from carbon dioxide, water, and renewable energy. Producing it at scale should be possible as soon as the early 2030s, and e-diesel is unlikely to face the same scale issues as sustainable biofuel, since the feedstocks—carbon dioxide, water, and renewable energy—are more readily available. E-diesel is a straightforward solution for OEMs and vehicle operators, because it is compatible with current internal combustion engines and infrastructure. However, like HVO and green diesel, it is forecast to cost twice as much as diesel in 2030.
Overall, most green electricity and green hydrogen solutions will require more frequent refueling, larger fuel tanks, or both. In addition, there is an inverse relationship between CO2 performance and operational complexity. The solutions that have a lower cost per ton of CO2 abated will likely be more difficult to implement. Hydrogen fuel cells are a good example. The technology holds significant promise as a way to virtually eliminate CO2 emissions—assuming the production processes are powered by renewable energy—but it would also require completely new engine designs and infrastructure for distribution, storage, and refueling.
Two Potentials Path Forward
To understand what’s possible in terms of technology and commercial viability, we recently analyzed the range of alternate energy sources and weighed them across four criteria: operational complexity, fuel performance, financial considerations (including capex, opex, and fleet replacement cycles), and overall environmental performance. We also talked to vehicle OEMs, engine manufacturers, oil and gas companies, governments, and fleet operators in a range of industries: mining, agriculture, and logistics.
Based on that analysis, we believe the transition away from diesel is possible and that it can be done faster than conventional wisdom might suggest—provided that companies can make well-informed tradeoffs. They can choose from two paths: either move rapidly away from diesel but pay more initially or migrate more gradually to alternative fuel sources but deal with more complexity.
The transition away from diesel is possible and can be done faster than conventional wisdom might suggest—if companies can make well-informed tradeoffs.
Speed and Ease—but at a Cost. Companies that want to move away from diesel immediately can transition to biofuel that is ethically sourced. Biofuels such as HVO or green diesel are available today and can be used in existing vehicle engines, requiring no changes to fleets or infrastructure and limited transition of the workforce. This approach allows companies to generate environmental gains starting today.
The catch with this approach is cost: HVO is two to four times more expensive than diesel. That difference will likely shrink over time, due to scale effects and other efficiencies, along with increased incentives, taxes, and regulations in some markets, but it still presents a challenge for companies that want to take immediate action.
Lower Cost but Greater Complexity and Time Requirements. With the right collaboration between energy producers and vehicle OEMs, net-zero solutions for heavy trucks will be commercially available in the next 10 to 15 years. Between now and then, companies can begin to implement these solutions as they become available, but they will likely need to accept increased complexity in several dimensions.
First, if the goal is lowest cost, companies probably won’t be able to use a single fuel for all vehicles and all applications. For example, battery electric power will be an option for light-utility trucks or pickups, but companies will need other solutions such as hydrogen fuel cells for heavier vehicles.
In addition, companies need to assess risks by asking some critical questions: which technologies are field tested and proven, which fuel supply chains are secure, and how can refueling downtime be minimized? They will also need to understand the cost implications of different technologies, along with timing: which technologies will be ready, how will costs for innovative technologies decline over time, and can those solutions be synchronized to fleet replacement cycles?
For companies that can manage these complexities, there is a clear competitive advantage to being first to market: they may be able to charge a price premium to customers for products that are truly green.
Notably, these two paths are not mutually exclusive. Different organizations may opt to apply both approaches depending on their timeline, operational requirements, and other factors. (See “Different Industries, Different Solutions.”)
DIFFERENT INDUSTRIES, DIFFERENT SOLUTIONS
Consider two hypothetical entities. The first is a mining company with a goal of net-zero emissions from diesel by 2030 and a 50% reduction by 2025. The company focuses on haul trucks, which contribute 40% of total emissions and are due to be replaced. Efficiency improvements will only reduce emissions by 10%—not enough for the company to achieve its sustainability goals.
Because the company’s mining sites include steep, long ramps, its trucks need significant power. In addition, it can access direct electrical power to the sites through renewable energy agreements. The sites’ remote locations make hydrogen production on or near location difficult due to limits on access to the water required for electrolysis and the difficulty of transporting hydrogen by road or rail.
After analyzing all factors, the company determines that the best approach in terms of total cost would be to replace its fleet over two timeframes: Initially, it will switch the majority of its diesel fleet to diesel electric powertrains and use HVO instead of diesel. It will pilot direct electric power to the rest of the fleet through overhead cables. In the early 2030s, it will transition from diesel electric powertrains with HVO to direct electric, thus creating a fully electrified fleet. Through this approach, the company can reduce emissions by up to 90% before 2030, with enough time to build the infrastructure needed and pilot the direct-electric trucks safely.
Next, consider an agriculture company that wants to reduce all emissions from off-highway mobile and stationary equipment, such as tractors, sprayers, harvesters, and other trucks.
Electrical infrastructure is available to recharge battery-powered vehicles, but farms require equipment to have long ranges and running times, which limits how long a vehicle can recharge (though renewable energy can be used to power some stationary equipment or light vehicles such as pickup trucks). However, HVO is a more feasible solution. Because HVO can be swapped in for diesel with no changes required to existing equipment, it offers the potential for immediate impact.
The company determines that the fleet will begin using 50% HVO by 2022 and complete the transition by 2025. Longer term, it will plan to pilot hydrogen power in several vehicles starting in 2030 (contingent on the development of that technology). Stationary equipment such as irrigation systems will be powered through electrification from renewable sources starting in 2023 and completed by 2025.
All heavy industry companies have a range of choices when it comes to mapping out which path to lower CO2 emissions will work best. A close look at logistics and daily operations can pave the way to a greener future.
A Need for Proactive Collaboration
Regardless of which path a company follows, it must also collaborate with OEMs, energy suppliers, governments, customers, and even competitors. For management teams at fleet owners and operators, co-creating the market in this way requires focusing on three main priorities—and continuing to reassess over time as technologies evolve.
Getting Started Now. The gradual evolution in fuel and vehicle technology means that the transition to cleaner fuels will happen over time, rather than through a single transformation. Accordingly, companies need to make informed decisions on how they will meet interim and end-state emission targets. Questions to consider include:
- Which strategy will we pursue: operational simplicity or lowest cost?
- Do we need a single solution for different vehicles and applications across the entire business, or can we mix and match?
- What is the total cost of ownership for each solution, factoring in fuel, new fleets, new workforce skills, and the storage and refueling infrastructure required for different solutions? When we factor in productivity elements such as vehicle operational time, how does this change the cost equation?
- How can I synchronize my fleet replacement cycles and interim emissions targets with various technologies as they become available?
Putting the Enablers in Place. Even after companies choose specific technologies, they need to plan for the transition in terms of coordinating pilots, retraining the workforce, securing the new fleet and fuel supply contracts, and building onsite storage and refueling infrastructure. For example, if a company opts for renewable electricity or green hydrogen, our analysis found that the electricity demand for a single fleet or site would increase by up to tenfold. This means companies must carefully consider how they will access such a significant increase in renewable power.
Forging the Right Partnerships. Solving these challenges will require companies to partner with OEMs, energy suppliers, oil and gas companies, unions, even industry peers, in order to find more cohesive, fit-for-purpose solutions. Building partnerships across the entire value chain for heavy vehicles and equipment will allow stakeholders to pool resources, combine expertise, co-invest in ways that minimize the risks associated with high fixed cost investments, and deliver sustainable outcomes at scale more quickly.
Industrial and agricultural companies have high aspirations to reduce their CO2 emissions, but they won’t achieve that goal without addressing the diesel they currently burn in their truck and equipment fleet. Our research shows that eliminating diesel is a feasible goal if companies are willing to either pay more for rapid change or make adjustments at a gradual pace and reasonable cost but with added complexity. Regardless of which path a company chooses, leaders must be willing to consider complex tradeoffs and take deliberate steps to change. With the right mindset, companies can begin rethinking their fleet today and put themselves on a direct path to a more sustainable tomorrow.