It might be easy to pass off the last few years in the semiconductor industry as just another example of its cyclicality. In response to a pandemic that seemed to augur lower demand for key products, global chip factory output was slashed. But when the falloff in demand never fully materialized, chip companies were forced to scramble—and it took them months to catch up to global orders. Yet even as chip supplies ramped up, new uncertainties impacted production and logistics. These include the economic effects of the war in Ukraine and unsettled trade dynamics between the US and China.
But what if those ups and downs are not just emblematic of the chip industry’s all too familiar cyclicality? Instead, perhaps this turbulent period in the semiconductor industry marks the beginning of a permanent era of increasing uncertainty—when supply chain imbalances will be harder to forecast and prepare for without taking proactive steps to stay ahead of the instability. This view seems more likely for one crucial reason: a series of structural industry shifts are amplifying supply and demand complexity, so much so that uncertainty will intensify and become the new norm within the semiconductor industry for the foreseeable future.
These shifts include the following:
- Increased pervasiveness of semiconductors, a core component now of virtually all commercial- and consumer-purchased goods and equipment
- Supply chain bifurcation, in part the result of geopolitical tensions that are hindering chip buyers from easily sourcing semiconductors across borders
- Slower migration to new nodes, or latest chip technologies, as the semiconductor industry continues to see growing demand for chips with more mature nodes
- The need to comply with regulations requiring monitoring and tracking of carbon emissions across the semiconductor manufacturing supply chain
As these fundamental changes alter semiconductor supply chains, chip customers in all industries cannot afford taking reactive efforts to weather swings in demand and capacity while waiting for good times to return. Instead, they must adopt ways to mitigate the persistent volatility through a series of proactive and protective steps. This would make them a more active participant in the industry’s direction and would ultimately ensure supply chain resiliency.
As structural shifts amplify supply and demand complexity, uncertainty will become the new norm within the semiconductor industry.
Semiconductor Pervasiveness
The most obvious structural shift in semiconductor supply chains is the accelerated ubiquity of chips in products of all types—from cars and computers to aerospace and defense, just for starters. For instance, between 2019 and 2021, the number of chips used in automobiles increased by an average of 40%, a figure that will continue to rise as electric vehicles, advanced assisted-driving systems, and fully autonomous vehicles become more commonplace. Similarly, the many appliances and equipment joining the Internet of Things and rapid advances in mobile phone features are further driving demand gains for chips. Viewed more broadly, the current $600 billion market for annual semiconductor sales is expected to reach $1 trillion by the end of this decade, according to a Nasdaq report.
Expanding chip usage only aggravates the dynamics that have made cyclicality a persistent factor in the semiconductor industry almost from its inception. The speed with which chip demand and supply move is drastically different due to inherent factors that are difficult to overcome. Demand in terms of either volume or chip designs can shift rapidly and often. But efforts to adjust supply almost always lag changes in demand because expanding capacity or reconfiguring production lines is time consuming.
This dynamic was front and center during the pandemic, when wait times for chips increased significantly as auto companies bent demand signals down—and then up—to satisfy unpredictable consumer demand during lockdowns. Responding to initial forecasts of a demand reduction, semiconductor suppliers reallocated capacity to stay-at-home equipment, such as PCs and mobile devices. When automakers began to increase their orders, chip companies couldn’t keep pace with the sudden uptick—and a bullwhip effect, in which supply failed to reorient to shifting sentiments quickly enough, was very much in play. Considering that we are likely to see many additional and unexpected demand increases combined with volatility in the coming years, any beliefs that semiconductor supply chains will become less stressed and more reliable are only empty hopes.
Supply Chain Bifurcation Due to Geopolitics
A partial bifurcation of global semiconductor capacity is occurring, brought about by international trade dynamics as well as the increasing perception by national governments that domestic semiconductor availability is essential for industrial competitiveness. This, in turn, is making it harder for chip customers to maintain access to global supply chains and is having a significant and likely long-term impact on supply and demand volatility.
The most obvious aspects of this can be seen in the many incentives implemented by governments to buoy domestic semiconductor production capacity and innovation and the increasing number of restrictions to prevent sales or exports to certain countries (see Exhibit 1).
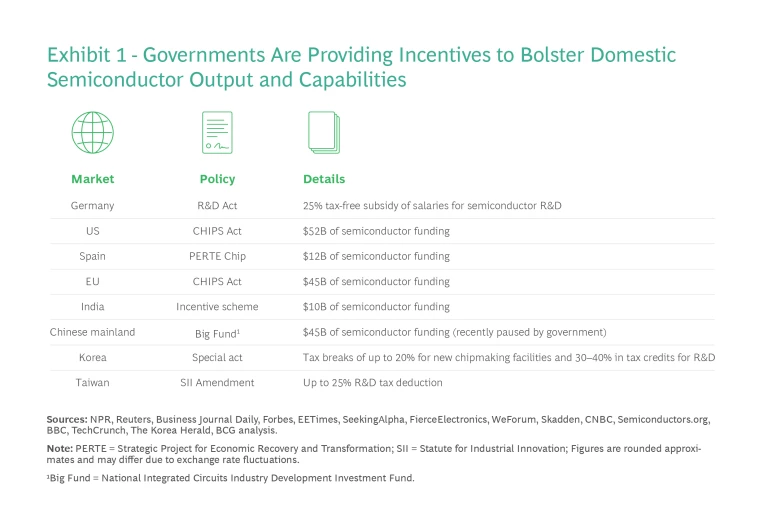
At the time of the writing of this article, noteworthy examples include the US Chips Act and the European Chips Act, which have earmarked $52 billion and $45 billion, respectively, for domestic semiconductor development. Spain and India are providing somewhat less support, while Korea is offering up to 40% in tax credits for semiconductor R&D. At the same time, trade constraints have bubbled up. The US has imposed chip export limitations targeting China, an effort joined by the Netherlands and Japan. And Russian technology exports from the US and the EU have been halted because of the war in Ukraine.
Slower Migration to New Nodes
Improvements in chip design and capabilities are a constant backdrop in the semiconductor industry, but now those innovations are contributing to intensifying and persistent supply chain volatility. While manufacturers’ planned investments focus on following Moore’s Law by making ever thinner, feature-rich transistors, the demand for older chip designs is not letting up—particularly as usage of mature chips in all products accelerates (see Exhibit 2). This is creating bottlenecks in certain chip categories.
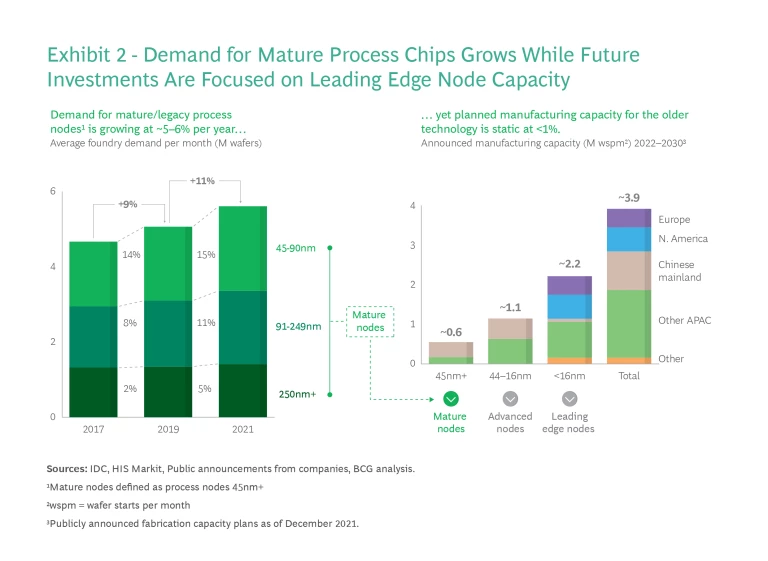
Indeed, demand for legacy chips produced in foundries has grown at about 5% per year since 2017, yet the annual manufacturing capacity increases announced for these semiconductors between now and 2030 are well below 1% per year. With these prospects, it is likely that there will be persistent supply challenges for mature nodes.
Tracking Carbon Emissions
No industry can ignore the need to decarbonize in the face of unrelenting evidence that climate change is a significant and urgent problem. Yet the semiconductor industry is problematic. Its intensive manufacturing processes result in some of the highest carbon emissions of any industry, equal to nearly twice Belgium’s yearly emissions. And as semiconductor technology advances, its emissions are increasing—even as other industries are reporting real reductions. Moreover, semiconductor manufacturing consumes outsized amounts of water and generates significant waste.
Meanwhile, regulators, investors, employees, customers, and activists involved in the semiconductor industry are getting impatient and demanding that—at least as a first step—chip companies develop ways to monitor and track their carbon footprint with verifiable and realistic environmental, social, and governance (ESG) reports. This has generated some action: in 2020, 65% of semiconductor firms submitted ESG reports with some emissions calculations, compared to only 24% in 2015. Some of these companies have set Scope 1 and 2 target reductions, which would cover organizational and manufacturing emissions as well as energy usage; a few have committed to net zero aims by 2050.
But while necessary, these initiatives will likely add to supply chain volatility, particularly as customers require more green solutions to meet their own goals to shrink their carbon footprints. That may shift some demand to a smaller pool of chip makers who can meet the decarbonization requirements quickly; however, these chip supplies may be limited. And at the same time, semiconductor manufacturers trying to transition to greener products may strain operational efficiency in the short run, adding further uncertainty to the volume of some chips.
Navigating the Volatile Supply Chain
Facing ongoing disruptions in supply chain consistency, chip customers must act to mitigate risks and uncertainties by designing strategies that smooth out volatility as much as possible (see Exhibit 3).
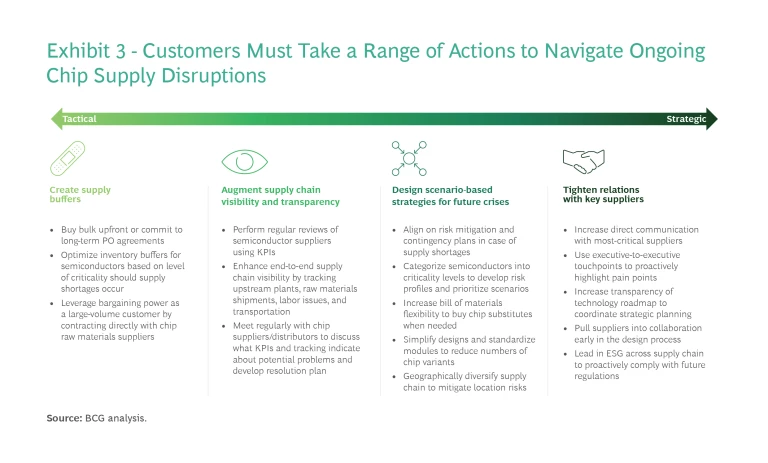
First, create buffers to supply disruptions.
There are several approaches in this category. A company could buy, say, a year’s worth of inventory up front. While this blunt force method certainly reduces supply risk significantly, it is a relatively inefficient tactical method that could lead to excessive inventory holding costs. A similar approach would be to commit to purchasing a specific dollar value of the most critical chips over a long-term period. This can help build a strong relationship with a few suppliers and provide chip makers with a good indication of future demand. Moreover, it can incentivize chip suppliers to increase capacity investments for certain chips or node processes, ensuring availability of specific types of semiconductors even if demand increases. For chip customers, as a general rule, it can be strategically beneficial to hold higher levels of inventory for essential chips that almost certainly will result in missed sales if a shortage occurs.
For instance, after the 2011 Fukushima earthquake, Toyota required suppliers to create inventory buffers of anywhere from two to six months for its most critical chips. As a result, Toyota was less impacted by COVID-driven supply volatility than many other automakers. Alternately, for chips that can be replaced or are less crucial, lean inventory management may be less costly and more effective, provided that multiple reliable sourcing partners are identified upfront.
Some high-volume, high-influence chip customers can ensure consistent availability of their most essential semiconductors and components by using their large marketplace presence to contract directly with chip materials suppliers and semiconductor equipment manufacturers. These purchases may be diverted to an integrated device manufacturer (IDM) or a foundry to manufacture the chips or may be used for in-house chipmaking capacity. Either way, they are a means to avoid the type of upstream gridlock that customers are usually at a loss to prevent.
Second, augment supply chain visibility and transparency.
This involves setting KPIs that will allow a company to detect anomalies or signals of supply risks at their suppliers well before they actually impact availability. These KPIs can include shipment lead times, cost increases, defect rates, on-time delivery percentages, new product release timeliness, and volume commitments of chip suppliers and distributors, to name a few. Chip customers should also establish internal KPIs to track overall organizational sourcing performance and expose impending problems. These metrics should gauge changes in inventory days, inventory-to-sales ratios, purchase volume forecasts, forecast duration, line-down frequency related to chips, and order accuracy.
Ideally, these KPIs should be managed by a robust digital infrastructure powered by artificial and machine intelligence, with visualization tools that provide full and intuitive visibility across the supply chain for all relevant parts of the organization. With such a complex value chain in the semiconductor industry, bottlenecks or supply constraints can happen at any point—from upstream front-end and back-end facilities to materials, labor, equipment, and transportation. If a potential problem is detected, it should be brought to the attention of the supplier immediately. Additionally, there should be regular non-emergency meetings with key chip suppliers, Tier 1s, distributors, and other intermediaries to report on what the KPIs reveal about impending issues that may arise and possible areas of improvement and to tightly align expectations for supply chain performance. Routine on-site supplier inspections may also be valuable.
Third, develop scenario-based strategies for managing future chip crises.
To effectively respond with agility to a semiconductor shortage, responsibilities and actions to mitigate the shortfall need to be crafted and implemented across the organization. This can ensure that teams and business units know what they are accountable for and the steps they need to take in the event of a supply disruption. Planning for different outcomes and scenarios is critical and must involve near-term contingencies—such as demand changes, allocation shifts, and macroeconomic swings—as well as longer-term strategic plans, including inventory management methodologies, product positioning changes, and supplier relations.
To facilitate these strategic actions, certain supply chain tactics can be helpful. One of the more effective tactics is simplifying product designs to limit the number of chip variants that have to be purchased. This can reduce the company’s vulnerability to supply disruptions for multiple types of chips. Simplification can be implemented through design modules, which are standardized modules that can be mixed and matched and reused from one product to another, preventing engineers and designers from needlessly “reinventing the wheel.” Or it can be adopted by using more generic semiconductors, as Nissan has done by changing the design of circuit boards to substitute off-the-shelf chips for specialty models.
Also valuable is Bill of Materials (BOM) flexibility, which typically involves identifying software that continuously searches for chip substitutes and their suppliers that can be utilized immediately if the preferred option is in short supply. However, BOM flexibility is generally feasible only if alternate possibilities are considered during the product design stage.
Mitigating location risks is also essential. In today’s world, where regional disruptions due to natural disasters or geopolitical dynamics and disturbances are not uncommon, semiconductor customers must protect their manufacturing capacity through geographic supply chain diversification. This could be done by sourcing chips from suppliers with operations in multiple regions, or by expanding the supplier pool through multi-sourcing critical components. Reacting to location risks and trade volatility, Apple is seeking to shift some of its chip supply from Taiwan Semiconductor Manufacturing’s current Taiwan fab to the manufacturer’s newly established foundry in Arizona.
Chip customers must actively collaborate with suppliers and upstream operations to help minimize difficulties and prepare for possible disruptions.
Fourth, tighten relations with critical suppliers.
Given the stakes and the challenges, semiconductor customers can no longer afford to keep a hands-off approach to supplier activities. Instead, they must be actively collaborating participants, ensuring that their suppliers do not face difficulties in capacity, output, or quality and are prepared for potential disruptions. Increasingly, this level of transparency, urgency, and communication may extend to distributors, raw materials suppliers, and semiconductor equipment companies—the upstream operations that often are invisible to chip customers but could impact their operations significantly if any hiccup occurs.
To proactively highlight and discuss solutions to pain points, monthly executive-to-executive touchpoints with key chip suppliers are vital. During these discussions, pertinent high-level sourcing challenges and concerns should be raised—particularly those concerning the quality of the companies’ strategic relationship, product roadmaps and timelines, and potential joint operations that could be useful. Among these aspects of the discussions, sharing long-term technology plans with chip suppliers is extremely important.
Subscribe to receive the latest insights on Technology, Media, and Telecommunications.
On a more fundamental level, supplier collaboration between product-level working teams should occur as early as the design stage. Chip suppliers can often add insight about alternative design modules or chips that are less likely to be affected by disruption, and this knowledge may lead to differentiation in the end product that improves manufacturing efficiency. Moreover, customers can enjoy cost advantages by making volume commitments in advance, and suppliers can better prepare for future orders and supply scheduling in the short- and long-term. Partnerships like these are more prevalent than ever, especially in the auto industry. Volkswagen recently announced a joint venture with ST Microelectronics to design chips specifically for VW’s vehicle software. And Ford and GlobalFoundries signed a non-binding agreement that includes research and development on chips for battery management and self-driving systems.
Perhaps the option that customers have not yet taken sufficient advantage of—but which carries significant supply chain risks for the future—is working with suppliers on their ESG programs. For chip purchasers, suppliers represent so-called upstream Scope 3 emissions, that is, carbon from activities outside of the company’s direct operational and organizational activities. As regulators up the ante on ESG reporting requirements and stakeholders demand progress towards net zero, chip customers and manufacturers will have to work together if they hope to meet stringent targets without adding to supply volatility, since they are accountable for each other’s emissions. By partnering on ESG-focused design solutions, these companies can monitor and possibly mitigate any potential supply chain disruptions from green requirements and goals.
Everything we have learned about the semiconductor industry during the past few decades leads us to one conclusion: yes, cyclicality will remain, but it will also be amplified and altered by a new set of emerging pressures and trends. Constraints and surpluses will vary by chip type, geography, natural and geopolitical disruptions, ESG considerations, and technological advances—and this lack of predictability requires chip consumers to prepare for future shocks and crises. Otherwise, they will be caught flat-footed and pay a significant price.
Only a sustained commitment to a robust supply chain resiliency strategy—along with routine inventory management strategies and buffers, more collaboration with manufacturers, geographical diversity, and continuous monitoring of crises and options if a shortage occurs—can alter the trajectory for chip customers. Effectively preparing for the next shock with strategic and tactical strength is essential for a competitive edge in an environment where unpredictability will almost certainly be a feature, not a glitch.