The Obstacle
Automobile OEMs and suppliers need to reduce manufacturing expenses, which comprise the largest portion of their operating costs. Forvia is no exception. The company, a top global supplier of vehicle interiors and other components, wanted to adopt state-of-the-art technology to create breakthroughs in effectiveness and productiveness and serve as a template for upgrading other core plants around the world. Implementing cutting-edge systems brought multiple benefits: the plant became more competitive and attractive for new project launches, more agile in coping with regional labor shortages, and more sustainable in its operations. These and other improvements in operational excellence enabled the company to keep production in close proximity to automotive customers in high-cost regions of the world.
Creating a lighthouse plant led to immediate cost benefits, serving as a model for future factories. To unlock the full value of the transformation, Forvia devised a plan to integrate new ways of working throughout the manufacturing process, including in material flow management and assembly.
Our Approach
To convert the existing factory into a lighthouse plant, BCG worked with Forvia to identify transformational changes and draw up plans to carry them out. The transformation incorporated changes in the following four key categories:
- Automation. The company replaced manual material flow processes with end-to-end automation, from inbound transportation to truck loading, and fitted the plant with automated guided vehicles, advanced robots, and AI to detect quality issues.
- Digitization. Forvia made operations and its supply chain completely transparent by gathering and consolidating data throughout the factory and moving it to the cloud, which allowed the company to adopt predictive analytics to optimize processes.
- Structural changes. As part of automating end to end, Forvia installed flexible assembly lines and moved inventory to a second-floor “dark factory” storage area, freeing up shop floor space for more productive activities.
- Sustainability. By switching to green energy sources and increasing energy efficiency, the company reduced the plant’s energy consumption enough to achieve carbon neutrality.
For the project, BCG assembled a team of engineers and manufacturing experts with deep industry, functional, management, and strategy know-how. The team assisted company leaders to define the vision for the project and map out the transformation journey. With company leaders, they pinpointed the use cases that would be the most transformative and cost-effective for producing end-to-end benefits.
The Result
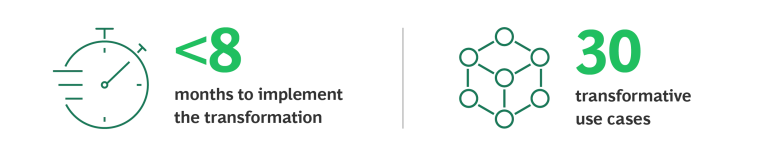
The BCG team worked shoulder-to-shoulder with key personnel in the plant to implement the changes, including developing standards and creating a plan to roll out changes throughout the organization so that the company can continue scaling on its own. Forvia adopted agile ways of working to implement the changes successfully in less than eight months. These changes created immediate value by reducing costs and shortening the ramp-up for vision control systems. Forvia also began deploying digital transformations to its other strategic factories around the world.
Learn More About Lighthouse Plants
Meet the Experts
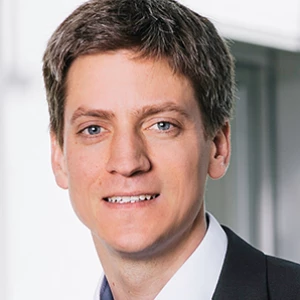
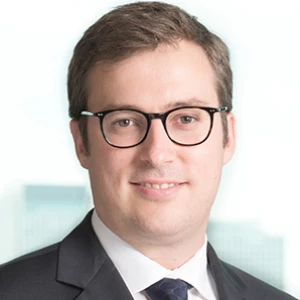
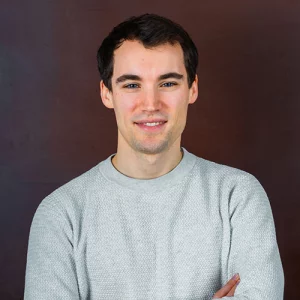
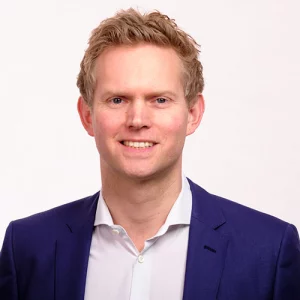
Explore Our Related Offerings and Insights
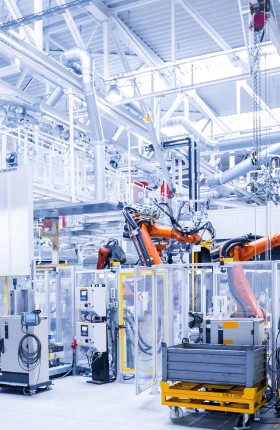
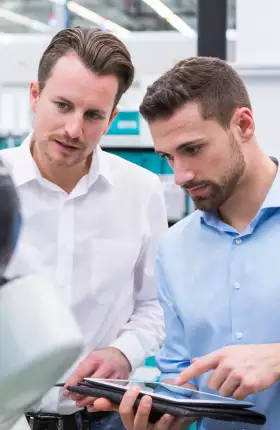
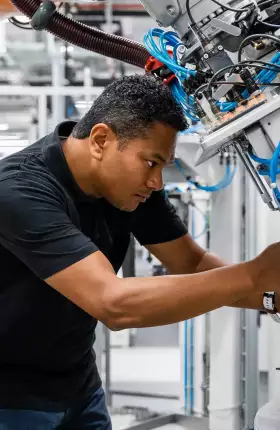