The COVID-19 crisis has interrupted the trade of goods and services around the world. Economic activity has been disrupted and global supply chains have broken down, highlighting an urgent need for companies to become more resilient – especially their supply chains (see Martin Reeves’ latest HBR article, A Guide to Building a More Resilient Business). A recent BCG global survey also found that 43% of companies plan to make permanent changes to their supply chain structures because of COVID-19. Supply chains are at even greater risk of disruption as the world experiences more frequent crises, making supply chain resilience an even greater imperative for Australian companies.
While many businesses recognise their supply chains need to be more resilient, they are still working out how to go about it. Most Australian companies have lean, just-in-time supply chains that are set up for efficiency but not for resilience, and as the COVID-19 crisis unfolded it had a disproportionate impact on Australian supply chains. To continue to win in a world faced with ongoing uncertainty, Australian companies are looking at how to modernise and digitise their supply chains while making smart trade-offs along the way.
True supply chain resilience comes from strengthening the strategic view of supply chains and investing in digital supply chain technologies. We have identified seven levers and questions for supply chain leaders to set their companies in the right direction, building resilience and helping to drive operational performance.
COVID-19 has highlighted the need for supply chains to be more resilient
The impacts of COVID-19 on the global economy are wide-reaching across trade, transport and supply of goods. In the early months of the crisis, 94% of the Fortune 1000 suffered supply chain disruptions. BCG estimates that global trade will fall by $3 trillion this year, from $18 trillion in 2019 to $15 trillion in 2020, with a return to 2019 values in 2023. Trade flows are also likely to shift dramatically (see Exhibit 1). The value of trade between the US and China is expected to fall, while trade between the US, EU, India and ASEAN is likely to increase. Australia’s trade patterns with some of its largest trading partners are also likely to shift, driven by an expected decline in the value of energy coal traded with Japan and Korea, and an expected increase in the value of iron ore traded with China and India.
Exhibit 1: Trade flows will look very different by 2023
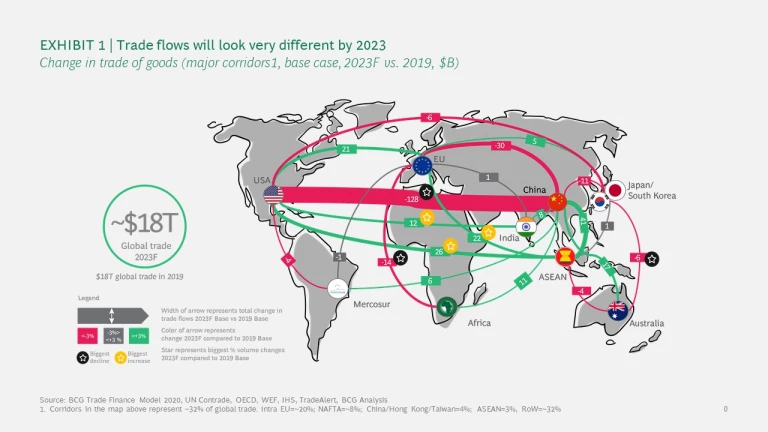
Many companies underestimated the risk of supply chain shocks and failures during the COVID-19 crisis, ranging from supply shortages to production stoppages. Major companies such as Apple, Hyundai and Airbus experienced critical shortages and had to close factories as a result.
These shocks are forcing companies to quickly adjust how they set up and manage their supply chains – while COVID-19 will pass, the more dynamic and unpredictable business environment, rising political tensions, and broader issues such as inequality and climate change, will all have direct and ongoing implications for supply chains.
A worldwide BCG survey in May 2020 found that 43% of companies plan to make permanent changes to their supply chain structures following COVID-19. When making these changes, they are considering design trade-offs that balance resilience with other dimensions such as cost efficiency, access, service levels and sustainability (see Exhibit 2).
Exhibit 2: Strengthening supply chain resilience requires companies to make trade-offs
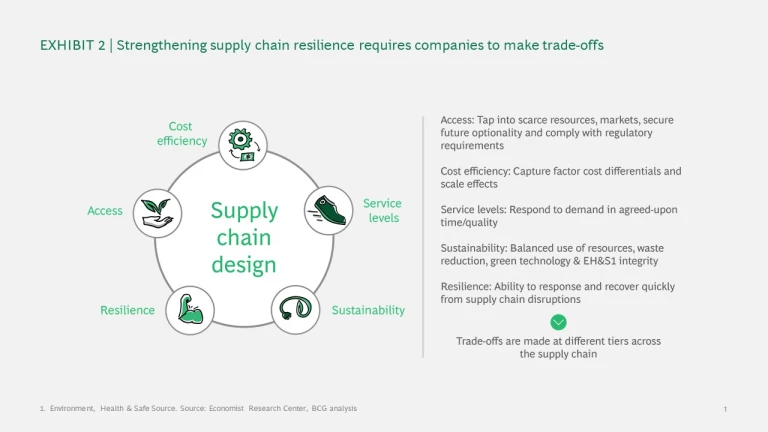
These trade-offs are seeing new supply chain models emerge, including migrated supply chains, (global supply chains shifting to new geographies to reduce geopolitical risk exposure) and regionalised supply chains (global supply chains moving closer to end-markets because of government incentives and/or risk mitigation). For companies in Australia, improving supply chain resilience and making the right trade-offs is even more important given the makeup of our economy, which depends heavily on imports for value-added goods.
Australia’s unique economic risks make supply chain resilience particularly critical
Looking at Australia’s post-COVOID-19 economy, BCG analysis shows that some sectors will rebound but others will face a much slower and more difficult recovery (How to Jump Start Australia’s Economic Recovery). Manual supply chains that lead to ongoing disruptions will leave sectors even more exposed. We have identified three factors behind poor supply chain performance. But it’s important to note these factors can be overcome.
Heavy reliance on imports across sectors
In the last 20 years, manufacturing as a share of Australia’s GDP fell from 13.8% to 5.6%.Australian companies rely heavily on imports for value-added goods in almost every sector, from finished goods (e.g., white goods, home appliances, clothing) to engineered components (e.g., components and parts for mining equipment, public transport, medical technology and construction). Import reliance, combined with low end-to-end visibility of production and shipping, and shocks at each step of the supply chain, left many Australian companies exposed and without the capacity or buffer to respond. The Australian rail sector experienced this recently when manufacturing plant shutdowns in Europe threatened the availability of critical, highly engineered switching components, with risk of network-wide shutdowns if supply hadn’t been resolved.
Dependence on a small number of global suppliers
To focus on cost efficiency, many Australian companies consolidated their suppliers, leaving few backups in terms of alternate suppliers for critical inputs. Combined with the COID-19 supply shocks, this led to many companies experiencing operational delays ranging from weeks to months. This is particularly critical given Australia is often the last stop on global supply chains. In the healthcare sector, COVID-19 exposed supply chains for securing critical medical consumables and equipment. Many major public and private providers didn’t fully recognise supplier risks or have alternate suppliers in the event of major disruption. In addition, few had end-to-end supply chain visibility, leaving them blind to stock levels and location of critical items across the network.
Reliance on integrated global supply chains and legacy systems
After almost 30 years of uninterrupted economic expansion, Australian companies weren’t facing the same impetus to modernise and invest in their supply chains that companies around the world were. Highly manual supply chains with low visibility of upstream and downstream stages persist, and a staggering 70-90% of Australian companies do not use common supply chain technologies (Swinburne Australian Supply Chain Technology Survey). When COVID-19 hit, companies without digital supply chains had to undertake urgent, manual assessments of their critical inventory to understand their business continuity risks.
Underinvestment in digital supply chain technologies has led to upstream and downstream challenges
A primary focus on short-term financial performance has led most companies to adopt a lean or just-in-time approach to operating their supply chains, combined with limited investment in digital technologies and a true end-to-end view. COVID-19 has exposed the direct risks of a just-in-time approach:
- Limitations in predicting and modelling consumer demand, combined with communications delays lead to uncertainty, miscommunication and missed opportunities
- Low downstream visibility of how goods are progressing along the supply chain creates unpredictability and can result in unmet demand for distributors and consumers
- Poor accounting of current inventory can leads to low levels of backup supplies of critical items, or lack of awareness on where the inventory is
- Limited ability to identify when upstream goods are manufactured and shipped results in unpredictable inventory levels and poor DIFOT performance (or at best communication or delays)
- Knowing which suppliers are likely to suffer disruptions delays the ability to secure alternate suppliers
- Uninformed purchasing decisions increases inefficient expenditure on goods
Manual supply chains may have delivered during decades of economic expansion and stability, but they will need to be more resilient to respond to global uncertainty. It’s time for companies to rethink their supply chains before the next crisis arrives.
Resilient, digital supply chains will set Australian companies up for the long term
Resilience is a supply chain design choice that senior leaders can pursue for greater stability and reduced risk. As with most design choices, resilience involves trade-offs; for example, a cost-efficient supply chain might prioritise low inventory levels, while a resilient supply chain might maintain higher levels of inventory to provide a buffer for critical items. These trade-offs may seem unnecessary when times are good, but they can be the difference between success and failure in times of crisis.
BCG has identified an opportunity for Australian companies to review their supply chains, and make strategic and process changes to be more resilient. Solutions often used in other parts of the world, such as on-shoring or re-shoring supply chain components in manufacturing, are not always suited to the Australian market. Instead, Australian companies have a tailored set of levers at their disposal to build supply chain resilience.
Seven levers for Australian companies to build resilient supply chains
For Australian companies to improve their supply chain resilience, they need to strengthen their strategic view of supply chains and invest in digital supply chain technologies (Exhibit 3).
Exhibit 3: Seven levers to improve supply chain resilience
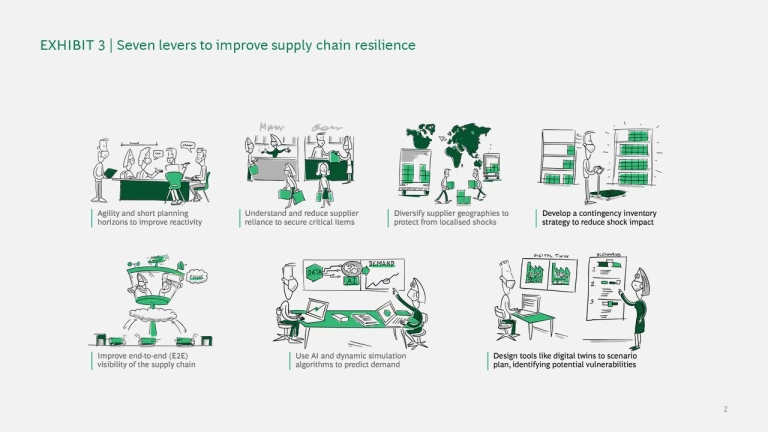
Strengthen the strategic view of supply chains
By going back to basics and auditing their planning, sourcing and inventory strategies, companies can build a more strategic end-to-end view of their supply chains to identify and close critical areas of risk. Companies can take four actions to do this quickly:
- Shorten planning horizons to react fasterCompanies can react rapidly to changing shifts in demand by shortening their planning horizons from months to weeks. Planning for the near term requires prioritisation, attention to critical SKUs, constant review, use of analytics to support decisions, and frequent communication. Successful short-term planning enables companies to respond fast to changing situations, and creates the ability to pursue innovative ideas and opportunities when they emerge.
- Diversify the supplier base for critical itemsA review of suppliers, particularly those that provide critical SKUs, will identify any limitations and risks to supply shock. This is particularly important for complex components, or where alternatives are challenging to source, buy or make. Diversifying suppliers will protect a company against the risk of a critical supplier being affected.
- Broaden supplier geographies to protect from local shocksMany companies have been forced by COVID-19 to setup supplies across more regions for backup capacity and redundancy. While some companies consider bringing manufacturing on-shore, having more suppliers in different geographies can be a more viable approach for Australian companies that want to reduce their risk to local supply shocks.
- Develop contingency inventory to reduce the impact of shocksCOVID-19 has exposed the vulnerabilities of just-in-time inventory management. This ‘optimal is operable’ approach improves efficiency and costs, but is highly vulnerable to shocks (see Martin Reeves’ HBR article, When Resilience Is More Important Than Efficiency). Re-thinking inventory strategy, particularly for critical supplies, can prevent major operational delays.
Invest in digital supply chain technologies
For a truly strategic view of supply chains, companies need to make their manual supply chains fit for today’s digital world. In a recent BCG survey, over three-quarters of CEOs said they plan to speed up their company’s digital transformation (BCG global Digital Transformation Survey 2020), and supply chains play a critical role in these efforts. Companies can take three actions to do this quickly:
- Implement a control tower to improve end-to-end visibilityA control tower incorporates an end-to-end view of the supply chain, using data from multiple sources to increase visibility, identify underperformance and improve coordination. A control tower formalises the decision-making processes needed to respond to volatility, and improve security and performance. Companies that have implemented supply chain control towers have reduced their downstream costs by 10-15% and their work centre costs by 3-5%.
- Use AI and dynamic simulation algorithms to predict demandAI and dynamic simulation algorithms take historical and emerging data and analyse it in real time to predict demand and improve supply chain efficiency. Using data can reduce inaccurate forecasting, including over- or under-ordering. Companies that BCG has helped to deploy machine learning and what-if scenarios have experienced a 10-20% increase in forecasting accuracy and 2-3x reduction in forecast bias.
- Employ scenario planning and digital twins to identify and react to potential shocksPlanning for scenarios when business is good or during a crisis enables companies to identify thresholds or trigger points and react quickly. Running the scenarios regularly will identify supply chain vulnerabilities and improve resilience. Digital twins – virtual replicas of a company’s supply flows – are a powerful tool in scenario planning and to help set parameters that identify when risk or disruptions occur.
It’s time for a supply chain re-set
As Australia moves towards the post-COVID new reality, supply chain leaders need to act quickly to review their own supply chains for resilience and avoid being left behind by the companies that have begun to make permanent changes to their supply chain structures.
To test the resilience of your supply chain, ask yourself the following questions:
Strengthen the strategic view of supply
- How responsive is my supply chain? How quickly can I make decisions?
- Do I understand my supplier reliance? Where are the critical risks?
- Where are my key suppliers located? Would diversifying geographies reduce risk?
- Do I have an inventory strategy? Does it consider the risk of future disruption?
Invest in digital supply chain technologies
- Do I have end-to-end visibility of my supply chain? Where are the risks and gaps?
- Can I predict demand? Where could I benefit from more powerful demand prediction?
- Do I have robust scenario planning in place? Could tools such as digital twins help me understand the potential impact on the whole business from shocks?
Asking and answering these questions will identify how your company can invest in a more resilient, digital supply chain that will protect against short-term shocks and improve operational results. With more resilient, digital supply chains, Australian companies can set themselves up to win in the future – no matter what that future looks like.