Industrial companies worldwide face the dual imperatives of achieving carbon neutrality and reducing costs. In our view, these imperatives need to be understood as one. Well-designed initiatives can simultaneously accomplish both objectives in a mutually reinforcing manner.
It is time to accelerate efforts. The industrial sector is directly responsible for almost 37% of global Scope 1 and 2 greenhouse gas emissions.
Many companies regard cost as an obstacle to curbing emissions, but ambitious decarbonization initiatives do not need to break the bank. Indeed, even companies that face the steepest obstacles to reaching net zero economically can find a lower-cost pathway to getting there. By pinpointing and fast-tracking levers that concurrently reduce carbon and costs, and combining emission reduction with operational efficiency initiatives, companies can generate savings to reinvest in less economical decarbonization initiatives. Some can even reach net zero emissions at net zero costs.
Companies Can Reduce Costs and Carbon
Almost all companies can apply a number of levers to abate emissions while reducing costs. The most relevant examples include:
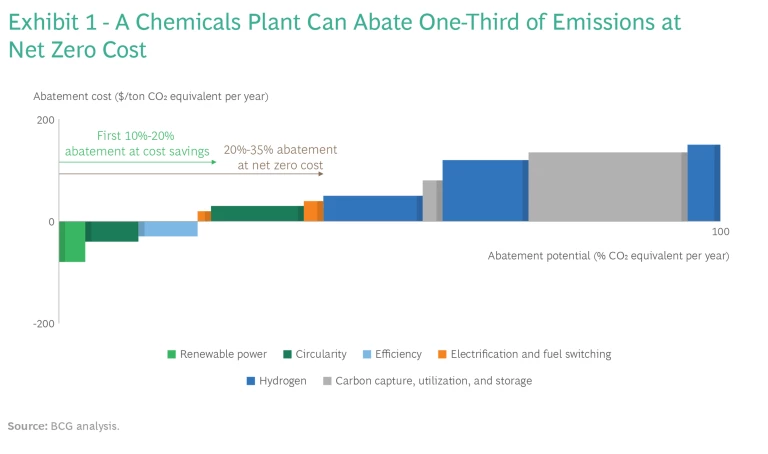
- Energy Efficiency. Implementing state-of-the-art processes in all aspects of production enhances asset utilization, improves equipment efficiency, and reduces scrap rates. Across most industries, it is not uncommon to see potential energy savings in the range of 20% to 30%.
- Renewable Power. Establishing on- or near-site renewable-power generation can reduce costs and exposure to fossil fuel price volatility.
- Circularity. Employing closed-loop processes reduces raw-material use and improves energy consumption.
Exhibit 1 shows the abatement curve of a chemical plant, highlighting that even hard-to-abate industries can implement decarbonization levers that also reduce costs. (For two case studies of how chemical companies can reduce their carbon footprint while enhancing their economic performance, see “A Middle Eastern Petrochemical Player” and “An Asia-Pacific Chemical Player.”)
A Middle Eastern Petrochemical Player
An additional 15% to 25% of emissions could be cut within five to ten years by employing waste-to-syngas conversion, CO2 capture, and mineralization techniques. Eliminating the remaining emissions would require carbon capture, utilization, and storage as well as power-to-heat technologies.
The company also identified the potential cost savings and capex avoidance associated with these decarbonization measures. In addition to ongoing cost savings, asset improvements and new asset installations that positively affect both cost and emissions saved capex compared with initiatives that separately address cost and emissions.
An Asia-Pacific Chemical Player
The project team identified and prioritized near-term "no regrets" decarbonization actions (spanning one to three years) that would achieve an additional 10% to 15% reduction. To achieve the remaining 35% to 40% reduction, the team explored new technology-based pathways, such as green hydrogen, bio-based methane, and carbon capture, utilization, and storage. These technologies are expensive, with costs exceeding $100 per ton, and require further investigation and monitoring. However, evidence points to the potential for considerable reductions as the technologies mature.
In the areas of energy and process efficiency, the team identified several levers with negative costs per ton of CO2 reduced, such as energy efficiency upgrades, temperature control, heat recovery, and gas recovery. Additionally, it found that electrification and on-site renewable generation would yield a positive business case over time despite requiring significant investments.
Although opportunities vary, the same principle applies across all major materials and process industries. (See Exhibit 2.)
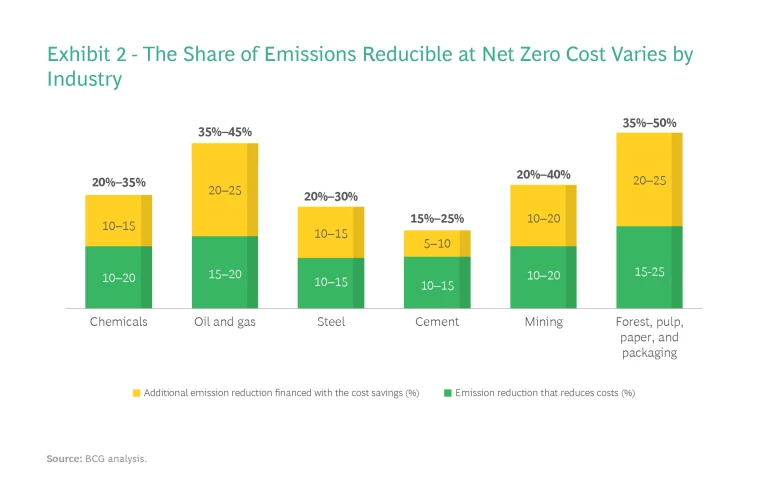
Navigating the Lowest-Cost Path to Net Zero
When implementing ambitious emission reduction programs, companies typically need to overcome three challenges.
The Technological Challenge. Many companies do not fully understand the lowest-cost combination of technologies required for net zero emissions. They have limited experience with designing and operating nonfossil heat generation and storage solutions with the lowest levelized cost of heat. In certain sectors, some technologies required for full decarbonization are not yet mature. Moreover, the availability and future costs of nonfossil energy carriers remain uncertain. Navigating these uncertainties requires strong technical expertise and broader knowledge of energy systems.
The Economic Challenge. When accelerating their efforts, many companies overemphasize the importance of decarbonizing their largest emission sources, usually heat generation. Although this approach might get them closer to, or even achieve, net zero, it usually will not do so at the lowest possible cost. Instead, companies should first maximize the yield from levers that are typically much smaller but more economically viable, especially those that can help fund the journey. At the same time, they should also maximize operational efficiency.
The Organizational Challenge. Achieving ambitious emission reduction targets economically is also an organizational challenge, especially for companies with multiple production locations. Companies need to gain transparency into asset performance and replacement cycles across a large plant network. They need to ensure that each plant identifies and implements the lowest-cost emission reduction pathway under its local conditions. And they need to create full transparency into capex requirements to enable optimal capital allocation throughout a network that may comprise dozens of individual facilities dispersed across many different countries.
A Structured Approach to Cost-Conscious Decarbonization
By taking a structured approach to decarbonization programs, companies can deploy resources cost effectively and minimize the timeline for improvements. To lead the program, they should establish a dedicated decarbonization task force with technical expertise that can support individual plants in developing their net zero pathways. Moreover, teams need tools to support their efforts, such as an industry-specific database of abatement levers, including their cost and typical impact.
By taking a structured approach to decarbonization programs, companies can deploy resources cost effectively and minimize the timeline for improvements.
To adopt a structured approach, we recommend a three-step process:
- Establish the baseline for a set of pilot plants. Select a few pilot plants for an initial evaluation. Develop a detailed baseline understanding of their energy consumption and emissions, operational performance, technology deployments, asset-level reinvestment cycles, and shop floor pain points. To build a fact base, conduct a comprehensive plant health check, analyze costs and plant KPIs, and review the technology portfolio.
- Design net zero and cost-out blueprints. For each pilot plant, identify and prioritize the cost-optimal combination of Scope 1 and 2 emission reduction levers—as well as cost reduction measures that will help fund the journey. Establish a medium-term technology and capex roadmap. Capture levers, methodologies, lessons learned, best practices, and common formats in a “decarbonization handbook” to facilitate rollout across the entire plant network.
- Roll out the program throughout the entire network. Develop cost-optimal net zero pathways through short sprints across the entire plant network, supported by a central task force. Design program controls that track progress, identify inefficiencies, and aggregate and prioritize capex investment requirements throughout all plants.
Companies should also establish stronger decarbonization governance. This entails integrating decarbonization into plant performance reviews (including the KPI system, tracking, and reporting), establishing clear targets and responsibilities, and gaining top-management commitment. Incentives and clear communication are also essential to maintain the organization’s pace.
Are You on Track?
Regardless of their current stage in the decarbonization journey, company leaders should know, or be able to develop, the answer to each of the following questions:
- Do we have net zero targets that are aligned with or exceed the targets established by the Paris Agreement and leading industry peers?
- Are we reducing emissions in accordance with our targets?
- Are we ensuring that every plant is maximizing the number of initiatives with a positive business case to achieve a cost-optimal net zero pathway?
- Are we adequately capturing lessons learned across our plant network?
- Does every plant have a concrete plan with specific initiatives to reach our targets
- Do we have full transparency into the business case of every plant’s net zero pathway—and the year-by-year capex investments needed to reach it?
- Do we track progress and the implementation of specific levers across our plant network?
- Have we integrated emission reduction into our targets, incentives, and regular performance dialogues?
For too many of these questions, a substantial number of companies cannot answer “yes.” By adopting a more systematic approach, they can raise their confidence in reaching their emissions targets and ensure that they do so more economically.
Industrial companies must prioritize the cost-effective achievement of net zero targets. By implementing strategies that maximize energy efficiency and then designing decarbonization programs that concurrently address costs, they can reduce both carbon emissions and operational expenses. The best efforts will maximize available funding for the ongoing journey. Embracing a cost-conscious approach to decarbonization also offers opportunities for driving growth and creating long-term value. Companies that succeed will promote a more sustainable future while maintaining or even improving their competitive edge.