AI is a force multiplier, transforming an array of industries, from finance to health care. But one area where it’s just getting started is field service: the complex and increasingly challenging world of equipment maintenance, inspections, repairs, and installations. Here, AI’s potential is particularly far-reaching. Now’s the time to tap it.
Whether it’s medical devices, utilities, industrial equipment, telecom, or trucks, the performance of critical assets depends on skilled field technicians operating in real-world environments. But the work is only getting harder. Equipment is becoming more complicated. Skilled labor is in short supply. And much of the knowledge that underpins field service is locked away in spreadsheets, tribal memory, or paper manuals. AI is uniquely positioned to change that.
Field Service AI by BCG X is a solution that helps predict failures, guide repairs, optimize dispatch, enable remote collaboration, and more. Companies employing it have increased the efficiency and quality of field operations, seeing 10% to 15% productivity gains and 10% improvement in effectiveness. Dashboards give visibility into technician productivity. Asset monitoring flags potential problems before they turn into trouble—and downtime. Additional features optimize scheduling, parts inventory management, and offsite support, among other functions.
AI is transformative, but to seize its full power, companies need to lay the groundwork. On the basis of our work across sectors, we’ve identified six success factors that separate AI leaders from laggards in field service transformation.
Six success factors separate AI leaders from laggards in field service transformation.
Establish a Unified Data Layer
The foundation of any AI system is data. In field service environments, where real-time decisions matter, it’s essential to bring together both live data and historical context. This enables advanced capabilities like predictive maintenance for HVAC systems based on sensor data (such as temperature, pressure, and compressor cycles) and historical service data.
But setting the stage isn’t easy. Companies need to integrate a wide array of data sources: IoT sensor data, repair logs, work orders, technician locations, equipment manuals, CRM records, and more. This data comes in many forms—structured, semistructured, and unstructured—and often varies by vendor, format, and department.
Companies that succeed start by identifying and connecting critical data scattered across equipment, workflows, and systems. They then organize this information into a unified, accessible data layer that AI systems can draw from—regardless of the data’s format or source. Typically referred to as a semantic data layer, it acts as an intermediary between data sources and users, providing a comprehensive and simplified view of data throughout an organization.
Tech + Us: Monthly insights for harnessing the full potential of AI and tech.
Design for the Edge Experience
The best AI solutions meet users where they are, delivering value without disrupting the task at hand. This is what drives adoption. Field technicians don’t work in offices. They operate in noisy factories, remote substations, and cramped equipment rooms—often with gloves on and with limited connectivity. Designing AI interfaces for these environments means going far beyond dashboards, creating immersive, intuitive, and hands-free experiences. Solutions also must be rugged and offline-capable.
Multimodal interfaces are critical. (See the exhibit.) Extended reality (XR) glasses can overlay diagnostic visuals during equipment inspections. Voice-to-text systems enable technicians to log issues without putting down their tools. Image recognition technology can identify damaged components and pull up relevant manuals. These interfaces enable technicians to get the information—and insight—they need, when they need it, without hitting the brakes.
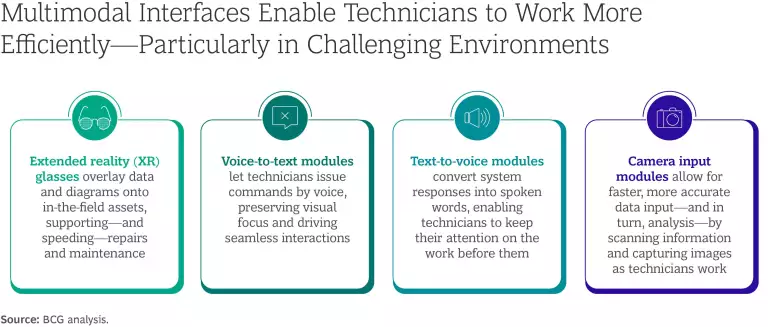
A large European rail operator used Field Service AI by BCG X to deploy XR glasses to support maintenance technicians. The workers could view assigned tasks, access procedures, generate tool lists, and reorder steps for efficiency—all hands-free. They also received real-time guidance from remote experts via video and voice chat. Within a month, experienced workers improved task efficiency by 20%, while newer technicians saw gains of nearly 30%. The company projects $200 million in savings over five years by extending XR to repair and refurbishment workflows.
Build Adaptive Systems That Learn from Field Experience
The field is messy. Conditions vary, sometimes greatly, depending on geography, climate, and asset. What works in a high-tech urban skyscraper may fail in a rural cold-storage facility. That’s why AI systems for field service must be adaptive—constantly learning, updating, and refining their outputs on the basis of real-world feedback.
This requires both technology and processes. Modern machine-learning operations (MLOps), a set of tools and practices, help organizations build, deploy, and update AI models efficiently without disrupting operations. Synthetic data and domain adaptation techniques aid in filling blind spots when real-world data is sparse. Federated learning enables localized model tuning on edge devices—a way for data residing on different devices, in different places, to collectively train AI.
Just as important: field technicians must be part of the loop. For example, if a model flags the wrong failure mode, the technician should be able to identify the mistake, and that identification should feed back into the system. This turns bias mitigation and model improvement into continuous, field-driven processes.
A large renewable-energy operator worked with Field Service AI by BCG X to deploy a GenAI-powered knowledge management product to assist field teams with service history lookup, job sequencing, and troubleshooting. By learning continuously from technician inputs and real-world usage patterns, the system became more accurate and context-aware over time. The results were measurable: a 5% to 10% boost in daily productivity for technicians and field leaders; a 15% to 20% reduction in job duration, increasing asset uptime; and a 10% to 20% improvement in rework rates for troubleshooting jobs.
Engineer Trust with Resilient, Explainable AI
Field AI systems operate in high-stakes environments. A misdiagnosis can mean a stalled train, a disabled emergency power system in a hospital, a compromised safety protocol at a chemical plant. In such scenarios, trust in AI isn’t optional—it’s essential.
Cybersecurity is paramount. With AI models deployed on edge devices, companies face expanded attack surfaces. Best-in-class organizations implement zero-trust architectures (where no user or device is automatically trusted and must continually verify their identity), monitor for adversarial behavior, and use AI-specific threat models (designed to detect and defend against attacks that target AI systems) to protect sensitive field data.
Equally important is explainability. Technicians need to understand why a system made a recommendation—especially if they’re being asked to act on it. To this end, best practices include embedding interpretable models, providing clear reasoning behind predictions, and designing interfaces that make decision logic easy to understand. Transparency drives trust, and trust drives usage.
Companies that embed explainability into the AI stack see faster, wider adoption—and bigger impact. Consider a global airline that integrated explainable AI models into its maintenance, repair, and overhaul (MRO) systems, demand-planning algorithms, and repair optimization models. When predicting component failures in aircraft engines, the system displayed confidence levels and factors contributing to its analysis. This empowered technicians to trust the output and escalate only high-risk cases. Forecasting accuracy improved by 30%, productivity across repair shops increased by 15%, and working capital for critical parts rose by 10%.
Companies that embed explainability into the AI stack see faster, wider adoption—and bigger impact.
Deploy Agentic AI to Automate and Coordinate Action
The frontier of AI isn’t prediction—it’s autonomy. Agentic AI systems are capable of planning, reasoning, and taking multistep actions with minimal human oversight. In field service, this can unlock transformational gains.
Imagine the following scenario. An AI agent receives diagnostic signals from an MRI machine. The signals reveal inconsistent image calibration, a serious problem because it can lead to misinterpretation of MRI scans. The agent compares the anomaly with historical maintenance records, identifies likely causes, retrieves the appropriate calibration procedure, preorders the necessary parts, and assigns a technician with relevant experience. This is not automation of a single task—it’s intelligent orchestration of an entire service workflow.
Right now, AI agents are mostly powering back-office automation, such as customer service chatbots. But new frameworks are making it possible to coordinate multiple agents across systems and processes, and this opens the door to all kinds of possibilities—and potential. As the technology matures, AI agents will expand beyond the back end and drive frontline collaboration.
But success demands careful design. The actions that agents take must be transparent and reversable. And AI agents must operate within defined guardrails. Without them, agents can take unintended actions or produce unpredictable outcomes.
Done right, agentic AI becomes not just a tool but a teammate. A leading processing-machinery OEM deployed the technology to boost production efficiency in its customers’ factory lines. AI agents gathered data scattered across production logs, sensor feeds, and quality control systems, as well as data relevant to contextual factors like shift patterns and raw-material batches. Acting as always-on assistants, agents helped engineers identify bottlenecks and anomalies, track equipment performance, and conduct advanced root-cause analysis. Over time, the agents accumulated historical knowledge of the plant’s behavior—effectively becoming a digital memory of operations. The solution improved line availability more than 10% by accelerating recovery from process anomalies and suggesting de-bottlenecking actions based on cycle-time analysis. And it sparked a 1% to 2% uplift in overall productivity.
Future-Proof the System with Modular, Scalable Architecture
AI is evolving quickly. Today’s models will be eclipsed in months, not years. Companies must design their field service ecosystems to scale, advance, and integrate new capabilities with minimal friction.
This means adopting modular architectures, where components can be upgraded independently. It means favoring API-first designs that simplify integration with third-party tools—whether it’s a new XR headset, an edge AI inference module, or a GenAI assistant or agent. And it means planning for hybrid infrastructure, with edge, cloud, and on-device intelligence working in tandem.
A leading truck-leasing company created a modular AI stack that could interface with mixed fleets of assets across customers, regions, and hubs. By standardizing APIs and using containerized ML models, the company enabled faster rollout of analytics tools for heavy, medium, and light assets—leading to a significantly faster deployment cycle. Crucially, the architecture was designed with GenAI extensibility in mind: components like service history summaries, technician copilots, and dynamic maintenance guides could be integrated without replatforming. This plug-and-play design ensures that as GenAI use cases mature, from troubleshooting chatbots to voice-guided diagnostics, the system can scale to support them, securely and efficiently.
None of this works, however, without investing in change management. Technology doesn’t succeed unless people embrace it. The next article in this series will explore how companies are building the leadership, training, and cultural alignment to drive AI’s use—and benefits—in the field.
AI is reshaping how businesses operate, but much of its power has yet to reach the frontline. Field service remains one of the most complex and critical domains in industry—and one of the ripest for transformation.
Companies that get it right don’t just adopt AI tools. They build AI ecosystems: integrated, adaptive, secure, and designed for the messy realities of physical work. The six success factors outlined here are the foundation for that ecosystem.
The prize? Faster service. Safer operations. Smarter decisions. And a workforce empowered by intelligence—no matter where they’re working.
The authors thank Shailin Shah for his contributions to this article.